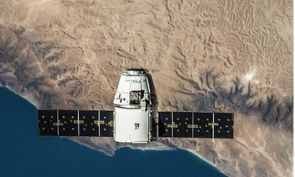
Data is eclipsing oil as the global economy’s prime resource. In the meantime, though, it’s the very thing the sector needs for optimum performance.
Five years have now elapsed since the Economist pronounced that “the world’s most valuable resource is no longer oil, but data”.
It is, after all, the fuel for the digital environment that permeates much of the industrial world. And without which, no process company has a viable future long term.
At the same time, the oil and gas industry has long faced a challenge from closer to home, in the shape of the growing pressure for renewable forms of fuel and energy to replace fossil sources.
And yet, if the writing is on the wall for oil’s dominance of all things economic and oil and gas’s central role within its key sectors, it is likely the decline will be measured in multiples of decades.
As with so much else, lockdown, Brexit and the ripple effects of the Ukraine conflict have simultaneously laid bare the dangers of relying on oil and gas and the short-term difficulties of turning one’s back on fossil sources, particularly those that lie within a country’s defensible borders and territorial waters
Plus, while the growth of the data economy and the rise of ethical investing may erode O&G’s once unassailable position, it is worth reminding oneself that the epitaph ‘data is the new oil’ predated the historic assertion from the Economist’s leader article by more than 10 years; having been coined in 2006 by Clive Humby, co-founder of the consumer insights giant dunnhumby.
While the push to renewables could conceivably constitute an existential threat to oil and gas, Big Data might undermine its economic pre-eminence but also provides the tools to maintain future relevance. And while the sector can only seek the most favourable adaptations to changes in the wider world rather than attempt to overturn them, it can itself determine how much it exploits the value of the data revolution.
Oslo-based Cognite specialises in software for asset-heavy industries including oil and gas, together with power and utilities, renewable energy and manufacturing, with a focus on converting ‘industrial data into customer value’.
Co-founder and chief technology officer Geir Engdahl explains the challenge for companies with well-established legacy assets and operations: “The businesses that can adjust their people and processes will have a first-mover advantage in this new data-driven era. Those that remain wedded to past investments will eventually have to shoulder twice the technology debt,” he warns.
“Unlocking the power of data will be key to ensuring companies can maintain business continuity, drive operational resilience and grab on to all the benefits they can from emerging technologies.”
The logic of this is easy to concede and most business have a wealth of the raw material required, in the shape of large quantities of data. Yet transformation may be easier said than done, acknowledges Engdahl: “Siloed data, outdated tools and shadow IT are the most common hurdles faced by industrial businesses. These are the barriers that companies need to overcome if they aim to democratise data and analytics, streamline collaboration and accelerate time-to-insight.”
Without the connectivity infrastructure to transfer sensor data from anywhere in the world, regardless of location, the value of IIoT falls dramatically
Alastair MacLeod, CEO, Ground Control
And in addition to the limitations imposed by company culture and structures, there are the issues of emerging skills and staff replenishment.
The global skills shortage needs no re-emphasis; it has been a given for years that developed economies have a preponderance of older workers and fewer younger ones. The rate of attrition in the workplace makes it imperative that automation and digitalisation are advanced as available workers reduce in number.
This presents a particular problem for the oil and gas industry. Younger potential recruits demonstrate a consistent interest in the energy sector, but that interest is often skewed in favour of renewables. And, while diversification and the introduction of sustainable practices can enhance O&G firms’ brand identity, they face greater recruitment challenges than most.
The Engineering Construction Industry Training Board (ECITB) workforce census (see Pumps feature, page 21) highlighted the problem – three times as many workers over 50 in the sector than under 30 years of age. And if recruitment fails to keep pace, it will need to be offset by retention and skills retraining.
Thankfully the days are past when environmental impact was seen as commendable but antithetical to business efficiency. In an era when ethics, regulatory demands and productive practices are seen as aligned rather than competing, effective data capture and analysis assumes greater importance.
Engdahl cites the example of one Cognite oil and gas customer, Aker BP: “[They] used machine learning smart monitoring systems to visualise all data relevant for trouble-shooting water contamination and identify factors related to high oil-in-water concentrations.
“This helped the company decrease its time spent on mitigating actions, a savings equivalent to an annual revenue potential of US$6 million. So, concentrating on user needs not only helps to unlock the power of data, it also drives operational resilience.”
Unlocking the power of data will be key to ensuring companies can maintain business continuity, drive operational resilience and grab on to all the benefits they can from emerging technologies
Geir Engdahl, co-founder and chief technology officer, Cognite
To some degree the problem lies not with an unwillingness to adopt and experiment – in some respects ‘traditional’ oil and gas outstrips process rivals such as biopharma (the subject of a recent Siemens digitalisation survey). Rather, problems may arise not from lack of adoption but from the piecemeal nature of it, explains Engdahl.
“Systems from multiple vendors, each paired with proprietary protocols, can lock down data, and these systems have an average lifespan of around 20 years,” he outlines.
“The impact of this mix of legacy kit, disparate control systems, non-compatible data models and communication interfaces can limit a company’s ability to collect and contextualise its data.”
A case in point was a client company with a portfolio of 30 platforms serving more than 300 wells but without an overview of maintenance activities within and between those assets. By bringing systems into one shared platform, scheduling and communications could be optimised, allowing effective, data-driven decisions.
The key, emphasises Engdahl, is understanding how people interact with data across the operation and to be aware of how the data needs to be presented to the various roles in the company, “maintaining a user-centric focus and having a solid foundation of scalable data”.
Alastair MacLeod, CEO of Ground Control [pictured], highlights another aspect that impacts on the achievement of joined up data systems in the oil and gas sector: connectivity.
“Given the often hostile and remote nature of the environments in which oil and gas plants are situated, the ability to monitor and analyse data, enabling quick, effective business decisions, and automation would not be possible without the rapid, real-time delivery of data,” stresses MacLeod.
“The biggest challenge is how that data is carried. Despite enhanced roll-out of faster wireless 4G/5G services, it’s estimated that only 15% [Businessinthenews.co.uk, March 2022] of the earth’s surface has cellular coverage.” Given the remoteness, vulnerability to weather conditions and relative inaccessibility over many O&G assets, satellite offers the most fail-safe option to ensure connectivity is not compromised, he argues.
“It enables companies to retrieve real-time data, from previously unreachable sites and provides a robust response should anything happen. Satellite connectivity, including the newer low earth orbit (LEO) satellites – which offer improved speed and ultralow latency to transmit sensor data back to SCADA software – is reliable, effective, and capable of bridging the gap between legacy technology and digital service evolution.”
Timely delivery of critical information negates the need for costly onsite visits in areas not serviced by 4G or 5G, diagnosing problems online before any production time is lost and costly breakdowns occur, adds MacLeod.
“From exploration through to drilling, hydraulic fracturing, flowback well testing production, artificial lift and enhanced oil recovery, satellite connectivity delivers accurate, real-time data for full operation visibility. Not just when it is needed, but autonomously.”
Reliable connectivity ensures not only the reliable supply of data but the effectiveness of data analytics that converts that raw material into value. Its implications could be far-reaching, points out Cognite’s Engdahl.
This could lead to the adoption of AI and machine learning to intercede in the operation of industrial facilities in complex use cases, such as where Distributed Energy Resources (localised energy generation) are deployed, he states.
As a starting point, though, oil and gas process operations must apply a threepronged approach, suggests Engdahl: tackle proprietary data protocols, concentrate on user needs and use trusted data sources.
Concludes MacLeod: “[The] industry has never had more sophisticated capabilities to optimise data capture and automate processes. But that comes with a caveat – without the connectivity infrastructure to transfer sensor data from anywhere in the world, regardless of location, the value of IIoT falls dramatically. Data gaps and interruptions can ultimately lead to poor business decisions.”