Climate change is shifting process safety parameters
12 Oct 2022
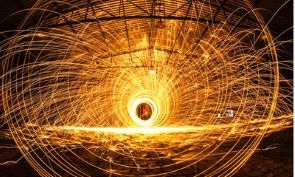
It is becoming increasingly difficult for sceptics to argue against not only the existence of climate change, but also its effect on our lives. What then is the impact on process safety, asks Carolyn Nicholls and Ben Taylor from RAS
The UK is not known for its extreme conditions, something welcomed by businesses operating with chemicals and other potentially hazardous substances. For instance, kerosene has a flashpoint of 38°C, and under this temperature, will not release vapours in a way that will be a flammable concern.
With the tame climates we are accustomed to in the UK, that flash point is typically not a concern. Yet, due to heatwaves, local ambient temperatures have recently exceeded 38°C.
Thus sites with small tanks of kerosene could have had moments where the ambient temperature was high enough, for long enough, to heat up bulk quantities to temperatures above the flash point. If it were spilled, a normally unexpected hazard (fire from ignition of the vapour) would then be present.
If temperatures reach levels where the wellbeing of workers may be compromised, changes must be made for operations to continue in a safe and ethical manner
Because temperatures historically have not been high enough to create these risks, sites holding high flash point fluids such as kerosene are not set up to deal with this risk. This could lead to further issues relating to Hazardous Area Classification and DSEAR, and in turn potential harm to the individuals working on sites.
It’s not only abnormally high temperatures that have caused issues in process safety. Winter storms have led to freeze events occurring in some parts of the world.
An example of this in the USA is the freeze in Texas in February 2021, which led to a major power crisis in the state. Many refineries and petrochemical facilities experienced equipment failures and process upsets due to the unprecedented cold weather, forcing several to stop operating, significantly hindering the refining and plastics manufacturing operations in the country.
Facilities can implement specific ‘winterisation’ or freeze protection practices to help reduce the risk of process upsets should an extreme freeze event occur. Though protective measures do exist, there is still a question mark over whether winterisation techniques are sufficient to cope with the higher frequency at which these extremes are occurring.
The human element
Human factors are primarily concerned with understanding people’s capabilities, and then applying this knowledge to the design of equipment, tools, systems and processes of work in order to provide working conditions which are safe and manageable.
Working in heatwave temperatures could have adverse effects on performance because full concentration is difficult to achieve under extreme heat, making mistakes more likely. These conditions could also potentially lead to problems for workers such as heat stress.
If temperatures reach levels where the wellbeing of workers may be compromised, changes must be made for operations to continue in a safe and ethical manner. This could include an increase in air conditioning or ventilation, or changing the processes which occur on site, which may not always be possible if a site is to carry out its primary functions.
With changes in climate showing few signs of levelling off or reverting to levels we are used to, action must be taken to ensure industry responds with appropriate changes in considerations for process safety.
- Carolyn Nicholls is managing director and Ben Taylor is process safety consultant for RAS