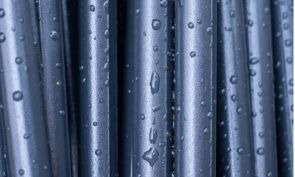
Fluctuating cost and supply is affecting not only industry consumers but also oil and gas from upstream to downstream, placing more emphasis on reliability, accuracy and sustainability.
Not surprisingly, carbon dioxide emissions took centre stage at the COP26 climate talks staged at the end of last year.
But for all the resolve shown at that event – which produced, if not unanimity, then a rare degree of common purpose – it is unlikely that the stated aims of the Glasgow Climate Pact, which resulted from the conference, will be met.
Of the near 200 signatories, almost three-quarters of countries representing 90 per cent of world GDP pledged to attain net zero emissions. However, given the diffuse avenues for CO2 release, this sounds at best ambitious.
More attention is being paid now to another emissions source. Methane has been identified by the Energy Transitions Commission (ETC) as a key contributor to improving the climate situation.
Oil and gas… will be vital for the energy industry to embrace green tech. Current technologies, which are not fully embraced by the sector, could be used to facilitate this green recovery
Tomas Karger, Marks & Clerk
As it notes in the announcement of its report Keeping 1.5°C Alive: Closing the Gap in the 2020s, “low-cost actions could cut fossil fuel related emissions by 60 per cent by 2030, while emissions arising from agriculture and waste management could be cut by 30 per cent”.
Over a century, states the commission, a tonne of methane emitted today has a ‘forcing effect’ impacting temperature about 28 times that of a tonne of CO2. While, over two decades, the relative impact is more than 80 times greater.
“The fact that methane is short-lived means that reducing methane emissions is the most powerful lever to reduce short-term temperature rises and risks of unlocking climate feedback loops,” it concludes.
Given methane’s key role in oil and gas, this will not be news to those in the sector but perhaps an indicator of more unwelcome attention to come for an industry that has struggled for acceptance and, thanks to rising fuel costs, is likely to face further criticism.
Offshore Energies UK’s poll of 1,000 secondary and 1,000 university students demonstrated a clear interest in careers in the energy sector as a result of a long-running news agenda on the subject.
Good news, given that UK industry faces a serious demographic issue with regards to recruitment: more older workers close to retirement, fewer younger ones. Drill down to oil and gas and it gets worse: Engineering Construction Industry Training Board (ECITB) statistics show the sector workforce is comprised of 54 per cent 30-49 year olds, 35 per cent over-50s and just 12 per cent under 30. In other words, three times as many near-leavers as starters.
Factor in the likelihood that young people interested in energy careers are focused on sustainable and renewable sources rather than fossil and the picture becomes more worrying – but not insurmountable.
During the height of lockdown, Tomas Karger of IP specialists Marks & Clerk pinpointed how O&G might align itself justifiably as a force for change.
“While renewable energy sources form part of [a] green deal, transitioning existing energy sources is also needed to facilitate this transition,” he stated. “The oil and gas sector will therefore be vital for the energy industry to embrace green tech. Current technologies, which are not fully embraced by the sector, could be used to facilitate this green recovery.”
And key to this are the innovations being made in pumps and flow applications in order to improve the use of better measurement and predictive analytics systems.
Upstream and midstream, much of the focus has been upon flow solutions with an emphasis on simultaneously addressing environment, producer costs and reliability.
Warrington-based sealing solutions manufacturer BiSN completed its 300th deployment worldwide this year, in the shape of the largest-ever bismuth plug – a contract for Aker BP in the Norwegian sector of the North Sea.
Though relatively brittle, as an alloy with cadmium or tin, bismuth is deployed effectively in fire extinguishers and electrics. It also has the benefit of providing a more environmentally friendly alternative to elastomer and cement options.
Says the firm: “Working with specially developed chemical reaction heaters to carefully melt unique bismuth-based eutectic alloys into plugs, BiSN developed its Wel-lok technology to create a bismuth plug that is not only safer, but much more reliable and easier to deploy.”
As well as providing a gas tight seal it boasts a density ten times higher than water, allowing the bismuth plug to displace well bore fluids.
Back onshore, Linewatch, the pipeline safety network combining leading oil and gas players and chemical firms, including Shell, Esso and Ineos, now operates a national database collating incidents.
While improved design materials have proven their effectiveness at winning incremental gains in efficiency, automated technology has allowed substantial gains
Linewatch manager Murray Peat notes there are an average of 300 reported infringements involving damage or near-damage to pipelines from unsafe working practices.
“Given that these pipes carry oil, gas or chemicals, any activity that either causes, or could have caused, damage to them, must be avoided. Not only does damage disrupt the supply chain, but it also puts the person doing the digging at significant risk of injury or worse – and has potentially huge environmental implications, says Peat.”
“We’re providing a big picture view of the whole country, covering all of the pipelines run by 22 of the UK’s biggest oil, gas and chemical companies. This collaborative information will help us spot trends, identify and then pre-empt risks… It’s a massive leap forward in pipeline and worker safety.”
For refineries and O&G sites, the high energy systems required for their work, coupled with constantly shifting process parameters, places particular demands on the assets employed.
Manufacturer Sulzer notes that the challenges of handling the abrasive media involved place great stress on the issue of reliability in the face of corrosion and other issues. Add to that, says the company, the fact that high energy means larger motors – a factor that has acquired still greater significance in the last year.
“Capital expenditure and downtime associated with the installation of new pump assets that may have differing foundation and piping requirements can stagnate efforts to improve equipment availability,” advises the company.
A less costly option is to assess and upgrade existing designs to improve durability and better limit maintenance price, it says, given that like for like part replacement will not ensure a different outcome.
While improved design materials have proven their effectiveness at winning incremental gains in efficiency, automated technology has allowed substantial gains in terms of prediction and the avoidance of downtime.
Increasingly sophisticated measurement techniques have overcome the issue of physical intrusion in downstream activities and the petrochemical sector. Ultrasonic flowmeters offer a non-invasive solution as they can be fitted outside pipes yet achieve high levels of accuracy.
FLEXIM enabled one French chemicals manufacturer to install a more cost-effective solution at its petrochem cluster for measuring ethylene gas for internal fiscal purposes; its existing gas station, which included a vortex flowmeter and density measurement, was susceptible to drifting measurement values caused by paraffin deposits from the ethylene. The company claims to have achieved 0.15% reproducibility of the measured value ±0.005 m/s for the client’s subsequent flow measurement.
Automated data collection and measurement feeds better prediction but greater progress depends upon a machine learning component within the process; building upon previously extracted data to make new, unprogrammed predictions.
But in order to be truly effective, point out Sulzer’s Dr Marc Heggemann and Seth Tate, such learning needs to be integrated at the highest level of a company.
Anlaysing asset health in high energy pumping systems employed in oil and gas, among other sectors, has the capacity to optimise operation and maintenance actions and so provide competitive advantages, they write, but: “Advanced analytics solutions that aim to improve business performance can only be deemed successful if they deliver a measurable benefit to safety, the environment or business finances. From the outset, the solution needs to be flexible and end-to-end capable, in order to deliver the business objectives.”
Using a digital solution to predict pump failure and perform remedial work involves providing solutions that “achieve the corporation’s goals and offer the flexibility to adapt to future changes [and so] require considerable system design expertise and historical equipment knowledge”.
Other issues to consider, they emphasise, are data security and data accuracy: data security policies vary from one company to another, they also evolve over time; and however effective data delivery is, ‘sanity’ checks to assess rather than assume data quality are an essential, they caution.