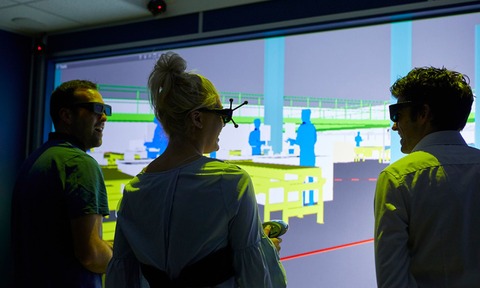
Though much talk about AI is in the future tense, it is already embedded in many areas, including industry.
As global leaders prepared to gather for two days of blue sky thinking and doom-mongery at Prime Minister Sunak’s AI Safety Summit towards the end of last year, two leading medical bodies provided a timely reminder that artificial intelligence also offers some very concrete benefits. Studies by the Royal Marsden NHS Trust and The Institute of Cancer Research published in The Lancet Oncology suggested that AI might be twice as accurate as the standard and invasive biopsy at grading the aggressiveness of some sarcomas. Result: faster diagnosis, more patients processed and more likelihood of successful outcomes.
Of course, one obvious win from AI does not negate the potential for the technology to be appropriated by malign actors, nor does it render concerns about the difficulty in supervising increasingly intelligent machines and systems irrelevant.
Research by the Institution of Engineering and Technology (IET) demonstrates that public nervousness about the future of AI and its implications remains deep, alongside some possibly over-generous faith in the range of its problem-solving abilities.
The IET-commissioned study of 2,000 individuals over a two-day period suggests that fear of the unknown – what AI can do on a macro scale allied with projections of dystopian eras ahead – lies at the heart of this. One third fear the implications for the future, more than one in three worry about privacy implications and four in 10 focus on mass unemployment resulting.
It’s important to recognise that AI has a longstanding presence and already forms the foundation of many daily activities
Dr Gopichand Katragadda, President, IET
The IET’s newly appointed President Dr Gopichand Katragadda acknowledges it is natural for individuals to have concerns about AI, given its proliferation in technical discussions and media. However, he cautions that “it’s important to recognise that AI has a longstanding presence and already forms the foundation of many daily activities”, citing those examples such as facial recognition on social media, map navigation and personalised recommendations as among the aspects people accept already in their lives.
On average, says the IET, the public appears to recognise the presence of AI in limited numbers of daily activities but underestimates the extent to which it is embedded in their own lives.
The many hidden touch points include, adds the IET, search engines (affecting 69% of respondents), social media (66%) and streaming services (51%), together with the likes of Google translate (31%) and autocorrect and grammar checkers (29%).
Yet, while respondents may be unaware of the degree to which AI is part of their lives, they display a substantial awareness of it as a positive force in improving not only healthcare (39%) but even more so, manufacturing (46%).
That could bode well for process sector employers in a period of more limited labour availability. Previous evidence gathered by Make UK and Sheffield Hallam university, in collaboration with Savanta has already revealed an overall shift in parental perceptions of the value of manufacturing careers for their children. The number with a favourable view has doubled in five years.
However, that may take time to influence things, says simulation software company Visual Components, whose October decision makers’ survey revealed more than a third of UK manufacturers reported new talent hire to be among their greatest difficulties.
The skills shortage has made it critical that manufacturers upskill current employees with supporting technologies to ensure that they sit at the centre of the production process
Mikko Urho, CEO, Visual Components
At the heart of this lies technology, it claims: skilled older professionals are departing at a higher rate than newcomers are joining and a substantial reliance on legacy equipment is unlikely to attract young digital natives. While employees are nowadays more likely to endorse new tech that can preserve their livelihoods, opportunities can be more limited. Less than half of the responding firms are currently training staff in new technologies.
“The skills shortage has made it critical that manufacturers upskill current employees with supporting technologies to ensure that they sit at the centre of the production process in the age of Industry 5.0. Deployment of robots, alongside digital solutions such as OLP and simulation software, can train employees in state-ofthe- art solutions and also encourage new talent to join the sector,” says Visual Components’ CEO, Mikko Urho.