Finding answers for those energy saving questions
12 Apr 2024
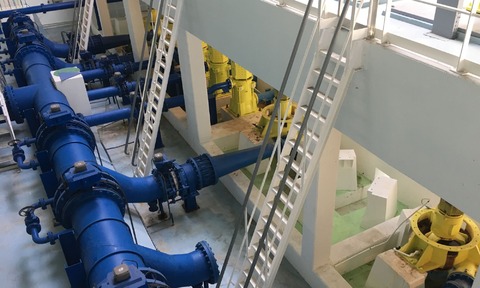
Just when you thought pressures could not get any greater, in comes another top-down mandate to reduce energy costs even further, because another massive bill for electricity has landed, writes Tom Clifford…
You’ve already looked at the pumps, which with their big motors, is an obvious place to start to try and make savings. Typically accounting for around 80% of electrical energy in process operations, knowing exactly how they are performing is of course, a key metric.
But if you’re restricted to sub-metering alone, then according to one optimisation expert, this is akin to putting fuel in your car, but never knowing how many miles have been driven.
Electrical sub-metering will give you some basics, and tick some KPI boxes, but it’s not going to give you anywhere near the full picture.
Computing the efficiency of a pump through measurements of differential pressure and temperature will give you a figure to work with,followed by the input power to the pump, which is usually obtained by measuring gross electrical power, and an assumption of motor efficiency.
Wwhilst this conventional, pressure-flow method of measuring pump efficiency is resilient for all head ranges from zero upwards, it is really only suitable and accurate for a test loop. For actual site use, this, with the absence of straight pipe in the individual pump main, immediately presents problems. Installing a flow meter on each and every pump is also too costly, and space constraints limit the accuracy of the application.
Another scenario that can prompt far more detailed performance evaluation will inevitably be related to ever increasing electricity costs.
It’s easy to describe such a frustration as ‘an opportunity’. Again, conventional methods of measurement have serious limitations, so a deeper dive into what’s really going on can sort issues once and for all, and create substantial savings, which is where thermodynamics comes to the fore
In essence, if you measure any two thermodynamic state variables (TSV), which include temperature and pressure, you can calculate any other TSV. For example, pump efficiency can be measured through a half-inch BSP (British Standard Pipe) tapping on each side of the pump, which is perfect for in-situ, on-site pump performance monitoring, and does not require the straight pipe lengths that conventional testing relies on.
Capital cost and installation costs of thermodynamic testing are lower and irrespective of pump size. Very importantly too, you’re going to get far superior accuracy at higher heads, measuring each pump, individually.
At one example, a food processing facility, annual savings of £20,000 were identified for the cooling system.
To evaluate the horizontal end-suction pumps, which are driven by a motor with an inverter drive (to allow control of the flow rate), we used thermodynamic measurement techniques, including suction and discharge pressures either side of the pump, differential temperature, and motor input power. This allowed us to calculate differential head across the pump, hydraulic efficiency, and volumetric flow.
Part of our work involved ‘throttling’ the pumps so that we could carefully observe the maximum possible flow through each pump under test, without altering the overall flow to the plant. Relative to the manufacturer’s typical performance, data showed that the shape of the pump curves indicated severe internal recirculation due to high wear ring clearances.
The advances that have been made in semiconductor electronics and hydraulic analysis methods can’t be ignored if you want to provide clear, compelling answers to that top-down mandate on reducing energy costs. Real-time pump monitoring with integrated decision support software is now readily available. It acts like a sat-nav, providing real-time instructions to help meet the minimum possible operating cost, even when system factors are changing.
Dr Tom Clifford is co-founder and CTO at Riventa.