Remote controllers at the helm
14 Mar 2016 by Louisa Hearn
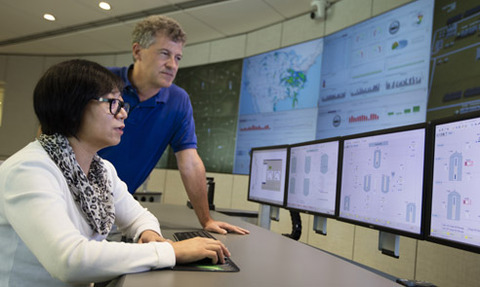
Control rooms are changing shape to accommodate a new breed of knowledge workers located far and wide, writes Louisa Hearn.
Once upon a time, almost every aspect of process plant operations took place onsite, and only a select few had a bird’s-eye view of production.
But new technologies have completely shaken up the traditional boundaries of plant management, opening the door to a very different way of operating.
We are entering the era of human centred design (HCD) says Jeff Dymond, business development manager for Oil & Gas Industry Solutions at Emerson Process Management.
This HCD concept challenges traditional business thinking about who should be in a control room, and how they work together to promote business interests.
Teamwork
“It’s not just operators anymore, but a cross-functional team that works together in the control room that might include operations, maintenance, logistics, quality, and production managers,” he says.
“They will be working together to make decisions that are for right now, not for the next shift or tomorrow.”
According to Dymond, this Integrated Operations Command Centre (iOps) will encourage the role of the operator to become less reactive and more proactive.
Instead they will seek to capitalise on opportunities such as strong market conditions, or spot potential equipment failure that may impact production targets.
It’s not just operators anymore, but a cross-functional team that works together in the control room that might include operations, maintenance, logistics, quality, and production managers
Jeff Dymond, Emerson’s business development manager, Oil & Gas Solutions
“For example, an integrated business operator in the iOps centre will understand that what was thought to be an optimised control loop may actually add cost to production by requiring more energy when you look at the entire process train,” he says.
Situation Awareness Graphics are another important concept being built into iOps Command Centres, says Dymond, which means data must be very easy to visualise to enable operators to understand the status of the entire plant or asset in a few seconds. It can also help them to visualise business information such as production yields or totals.
This means the iOps team is only alerted to situations that need attention, instead of monitoring the entire plant simultaneously.
“In the old days operators could handle up to 150 control loops and 500 indicators. Now with situational awareness graphics and the new iOps cross-functional team, they can be looking at 500 to 1,000 control loops and thousands of indicators,” says Dymond.
In the loop
Andrew Evans, technical director for automation trade association, GAMBICA, agrees that there is a limit to the number of control loops a single operator can cope with.
“As we drive further into the establishment phase of industry 4.0, the exponential increase in the number of low cost selfpowering sensors means that there will be a huge increase in the number of variables measured and therefore controlled, therefore many non-critical loops will not be monitored, leaving only the critical ones,” he says.
Another big growth area he observes are technologies that enable workers to operate remotely from the plant.
“Particularly in high wage economies in the west, the necessity to run as efficiently as possible to survive means that if operator costs can be reduced by using remote monitoring, then plants have to do it,” says Evans.
Raising barriers
Tighter controls on emissions such as the Industrial Emissions Directive and other environmental legislation have also meant that most process industries have to measure more variables.
“Traditionally these would have been expensive to monitor locally but advances in industrial wireless technology has meant that remote locations, physical obstructions, high installation costs or lack of existing infrastructure are no longer the barriers that they once were,” he says.
Dymond agrees that today’s process professionals don’t always want to work where their job is located, especially in dangerous and often distant and dirty environments.
However, for those that must be located at the plant, emerging technologies are also making their jobs easier.
“For mobile workers we now think of hard hats with heads up displays that not only display information to mobile worker but can be used to read information.
“You can also send things like work orders or an instructional video on how to replace a part in a pump,” he says.
“Using augmented reality technology, they may even be able to spot that the pump’s bearing temperature or vibration is getting a little high by looking at the pump as they walk by.”
Remote monitoring and collaboration are also a growing area of focus for ABB, says Dan Overly, global product manager of the company’s Oil, Gas and Chemicals business unit.
“By providing remote services, we can also help reduce the number of people offshore or reduce requirement for manning some completely in especially remote areas
Dan Overly, global product manager, ABB’s Oil, Gas & Chemicals business unit
“Everyone is trying to make sense of chaos, so our mission is to make information actionable – to put it into hands of people who need it – and that requires data analytics,” he says.
As well as boosting plant efficiency, ensuring health and safety regulations are critical to the oil and gas industries, says Overly.
“We have algorithms that will give indications of performance for a range of functions including alarms, safety and cyber security.
“By providing remote services, we can also help reduce the number of people offshore or reduce requirement for manning some completely in especially remote areas.”
An example is the floating Goliat oil production and storage facility in the Arctic Circle, being operated by Eni Norge.
ABB is supplying a wide range of services and equipment to the platform, including control systems, emergency shutdown, process shutdown, fire and gas detection and power management systems.
Three extended operator workplaces have also been delivered as interfaces to all systems, and these also enable remote operations from the shore.
A training simulator also allows staff to practice their responses to various situations that might arise on the platform.
Equipment: Eye on the prize
How to locate and visualise the most important set of production data is one of the key challenges for those in charge of keeping operations running smoothly.
This is something Honeywell Process Solutions has devoted much development time to, says Andrew Stuart, product manager of Control Rooms at Honeywell Process Solutions.
Last year the company added an auxiliary equipment unit with hard-wired switches, giving operators the option to manually shut down certain processes.
“Many critical industries like to have a level of protection beyond the control system if things go wrong,” says Stuart.
The company has also extended its Orion console to include three operating positions.
“Now we have all that screen ‘real estate’ for operators, we are now looking at better integrating tools and applications,” he says.
Many critical industries like to have a level of protection beyond the control system if things go wrong
Andrew Stuart, Honeywell’s product manager of Control Rooms
One of the key challenges is segregating the control system from the business network, where office applications run.
“These are often displayed behind the operators, or on a screen at the end of console,” says Stuart.
“So operators would be looking behind them 50% of time.”
To address this, Honeywell has shifted business applications to screens in front, without integrating them into the network, so operators can still have their eyes on the control systems when responding to email.
Honeywell has also recently launched its new Dynamo alarm management software that combines its operations management software with alarm management features.
The company says alarms can be reduced by up to 80% using Dynamo, while reducing root cause analysis time by 60% compared with conventional methods.
Extending its reach, the company has also recently launched Honeywell Pulse, which publishes performance alerts directly from the Dynamo software to a smartphone, allowing operators to monitor processes and take various corrective actions to address the situation while in the field.