The small matter of nanomaterials safety
21 Mar 2016 by Rob Smith
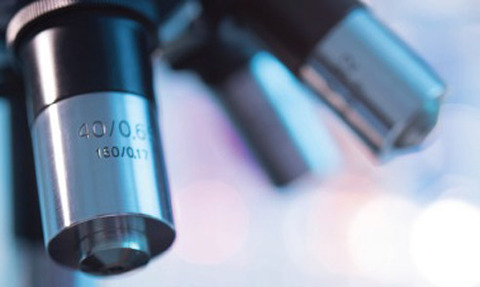
Nanomaterials have the potential to ignite, explode and cause serious damage to human health. Therefore, safety experts are working tirelessly to manage the risks and reduce the likelihood of harmful exposure. Robert Smith reports.
The Health and Safety Executive’s (HSE) archives are chock-full of information dedicated to the safe handling of materials commonly used throughout the science and engineering community.
Yet although working with nanomaterials isn’t considered a ‘new science’, the guidelines which seek to govern their use are.
“In 2009 university safety practitioners realised they needed agreed guidance for those working with nanomaterials,” says David Kinnison, faculty & chemistry safety adviser at the University of Southampton.
Until 2012, researchers only had access to a range of safety guidelines from individual research establishments, he says.
Guiding the way
Therefore in 2012 the Working Safely with Nanomaterials in Research & Development guidance was published by the UK Nanosafety Partnership Group – now the UK NanoSafety Group (UKNSG). The guidelines are also endorsed by the HSE.
Kinnison, who is also co-author of the nanomaterials safety guidelines, says the UKNSG wanted to create practical guidance for laboratory researchers that was authoritative and could withstand academic scrutiny.
“We began by corralling information used in the US and Europe and we pulled together different pieces of research and information to create uniform guidance for the UK,” Kinnison says.
Kinnison says the group is now ready to launch a second edition of the guidance, having reviewed the literature and shared its initial findings.
The need for such guidance clearly suggests there is a safety concern regarding the use of nanomaterials.
Aravind Vijayaraghavan, a lecturer in nanomaterials at the University of Manchester, says safety concerns arise in part because of the size of the particles that make up nanomaterials.
“When you have particles at the nanometre scale they become comparable to, or smaller than the size of individual cells,” Vijayaraghavan says.
“Therefore, a lot of research is being conducted to understand what happens when nanoparticles are in the air – which means they can be inhaled, ingested, or come into contact with the skin,” he adds.
When we make and handle nanoparticles in the lab there is certainly a chemical risk relating to fire and explosion
Aravind Vijayaraghavan, University of Manchester nanomaterials lecturer
However, Vijayaraghavan says one of the first precautions to take when handling nanoparticles is to make sure they do not get airborne.
“That can be achieved through correct handling,” Vijayaraghavan says.
“For instance, we handle nanomaterials inside a fume hood and we wear gloves, facemasks and appropriate personal protection equipment inside a confined space so airflow is minimised.”
Vijayaraghavan also says nanomaterials pose a fire and explosion risk.
“When we make and handle nanoparticles in the lab there is certainly a chemical risk relating to fire and explosion,” he says.
“It is a hazard issue we must always consider when developing a process such as creating a new nanoparticle or nanomaterial. We have to look at all the chemicals we use and the potential reactions and try to understand if anything is going to explode or create hazardous or exothermic reactions.”
Meanwhile, Barry Park, director at GBP Consulting, says a major part of safely working with nanomaterials and particulates is risk management.
“If you understand the potential hazards and have conducted adequate exposure assessments you can then put appropriate risk management controls in place.”
Park says some of those working with nanomaterials may have to consider creating a more suitable engineering facility that is better equipped at minimising exposure to nanomaterial hazards.
“However, organisations are now much better than they were at effectively managing risk. They are now far more aware of the risks of handling nanomaterials,” he says.
“Unfortunately, though, nothing can ever be 100% bullet-proof.”
If you understand the potential hazards and have conducted adequate exposure assessments you can then put appropriate risk management controls in place
Barry Park, director at GBP Consulting
Control of Substances Hazardous to Health (COSHH) assessments exist so those handling nanomaterials do so as safely as possible, and require employers to rigorously control substances that may be hazardous.
A COSHH risk assessment seeks to discover potential health hazards; how to prevent harm; how to ensure control measures are adhered to; and provides information, instruction and training for employees and others, among a number of in-depth parameters which can be accessed via the HSE.
“We have to try and consider every possible hazard…that is why we have COSHH forms,” says Vijayaraghavan.
“All the risks have to be identified as best as possible,” he adds. Meanwhile, disposal of nanomaterials, of which there is currently no waste regulatory framework in the UK, presents its own challenges.
At your disposal
The UKNSG guidance covers safety concerns relating to the disposal of nanomaterials and Kinnison says the group sees safe disposal as part of the COSHH process.
“You have to think about treating waste nanomaterials and disposing of them safely,” he says.
In terms of disposal, Kinnison says it is best to err on the side of caution and therefore nanomaterials are generally incinerated after use.
“However, when production is scaled-up to a more industrial level I think you will see new developments in the recycling of so-called ‘waste’ nanomaterials,” Kinnison says.
He says recycling in general is increasingly becoming a strategy employed throughout higher education.
“There are almost certainly going to be new opportunities in disposal because certain nanomaterials are very expensive to produce and if they can be recycled manufacturers would consider it. This is a very progressive issue.”
Technology – safety solutions
Best practice guidelines suggest nanomaterials should typically be handled within enclosed units, and dispersed in a solvent or embedded in a composite so as to reduce the risk of exposure.
“We err on the side of caution in the laboratory and try not to handle nanomaterials in dry form,” says Aravind Vijayaraghavan, lecturer in nanomaterials at the University of Manchester.
“If you have graphene inside water in a bottle, for instance, the number of ways in which you can be exposed to it is minimal.”
Experts are also devising inexpensive means of safely handling nanomaterials.
“A member of the UK NanoSafety Group (UKNSG) has developed a system that is essentially a Perspex glove box with a HEPA filter,” says David Kinnison, UKNSG chairman and faculty & chemistry safety adviser at the University of Southampton.
“The idea is you work with no air flow and can manipulate nanomaterials that are airborne. But you have containment, and once you are finished a fan extracts the contents and the filter retains the residual airborne material safely.
“Although you have effectively just modified the design of a box and added a filter, it is a simple and effective measure for reducing the risk of exposure by separating the operator from the hazardous materials,” Kinnison says.
Chemicals – bad chemistry
As chemical supply chains extend around the globe, even a minor chemical incident can wreak havoc. This is especially the case when companies and their staff are ill prepared for such an emergency, says Jon Gibbard, practice director at UK’s National Chemical Emergency Centre (NCEC).
“We find people tend to get very familiar with certain chemicals. Then when they come across a new chemical, they may not think clearly about some of the risks.”
For instance, they might be storing an oxidiser next to a flammable substance, creating a hazardous situation without thinking, he says.
“You need to conduct some careful thought and planning in regard to the different chemicals on the site,” says Gibbard.
Higher risk
When dangerous substances are scaled up to full production, there is an even higher potential risk if something goes wrong. While dangerous chemicals are often the most problematic, “even milk can be hazardous in a large volume in certain environments,” says Gibbard.
“We take about 7,000 calls globally per year, and on average must deal with one medical case, one chemical spill and one fire every day across our customer base. Fortunately we don’t have a number of high hazard incidents, but when they do happen they are significant.”
We find people tend to get very familiar with certain chemicals. Then when they come across a new chemical, they may not think clearly about some of the risks
Jon Gibbard, UK’s National Chemical Emergency Centre’s practice director
Such incidents often happen as a result of human error, says Gibbard.
“Someone might plug in the wrong valve and create an overflow, for example.”
In 2014, GE’s Druck plant in Leicester was ravaged by a major chemical fire resulting from a chemical reaction that caused spontaneous combustion.
It is in this situation where having an emergency plan becomes critical, and Gibbard suggests that all companies should communicate ahead of time with their local fire brigade if they have a potentially hazardous chemical on site.
There can be additional dangers for those working on the research and development of new substances says John Butcher, consulting team manager at Dekra Insight Process Safety.
Health effects
“Many new chemicals, such as active pharmaceutical ingredients (APIs), can by design have extremely potent health effects, and these need to be considered during all activities in the process area.”
Researchers must be careful not to expose themselves to the very hazards they are trying to prevent, by contaminating their equipment, “or by igniting an explosive atmosphere with a camera flash,” he says.
Vahid Ebadat, chief technical officer for Dekra Insight Process Safety, says that while most companies involved with highly hazardous chemicals have adopted effective models to manage chemical safety, Dekra continues to see many serious and catastrophic incidents each year.
“Leaders must create a culture that focuses on identifying exposures, acting on them before events occur, ensuring that hazards are fully understood.”
Louisa Hearn
Readers' Comments
There are no comments on this article, leave a comment below to have your say
Have Your Say
The comments have closed for this article