Data is driving the industrial IoT
9 May 2016 by Rob Smith
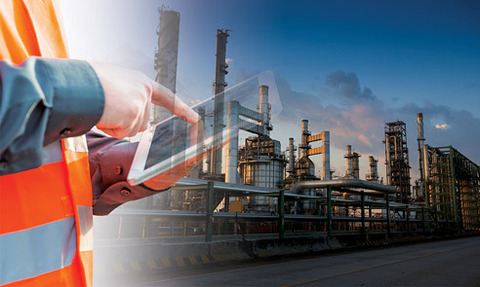
Plant operators are integrating more data technology to gain a better understanding of their facilities, writes Robert Smith.
Buzzwords like the ‘Internet of Things’ (IoT), ‘Industry 4.0’ and ‘Big Data’ are being bandied about with increasing frequency throughout the process industries.
But at the heart of these concepts – Big Data in particular – lays the acquisition and analysis of billions of data points, which can be interpreted to maximise production, enhance safety or transform maintenance procedures, to name just a few.
The acquisition and analysis of billions of data points…can be interpreted to maximise production, enhance safety or transform maintenance procedures, just to name a few
Greg Todd, sales engineer at data acquisition and analysis systems provider HBM, says data acquisition instrumentation is being used to benefit the process industries as a diagnostics tool.
“To examine a fault condition, customers might want to utilise a data acquisition device to monitor a certain procedure on one of their machines,” Todd says.
“Data acquisition devices allow them to analyse their processes and work out whether they have an issue.”
Close monitoring
Another area where data acquisition is benefiting the process industries – and one which Todd says is potentially the most important – is to conduct condition monitoring.
He says there is real interest in using data acquisition technology as a black box recorder to understand processes.
“Effectively, plant operators can go into their existing infrastructure and they can monitor additional parameters or else look at a specific component,” Todd says.
“When anomalies occur, an action can be set, which informs the right maintenance people.”
Todd says this type of condition monitoring is being used to help plant operators gain a better understanding of when something is likely to break down, which adds value – particularly if they are operating ageing machinery.
“Typically, a manufacturer will tell you their machinery lasts for 20 years, for example. However, the operator often needs to know if it’ll last another 10 years after that,” Todd says.
“With data acquisition you can find out if the machine can still be in service or if it actually does need to be switched off.”
Via data analytics software, an operator or maintenance manager can remotely view all the process plants their company operates
Data analysis, meanwhile, is being used to assist data acquisition within a plant.
HBM’s software division is set up to handle post processing data, which allows its clients to manipulate terabytes of data, Todd says.
Its Glyphworks software, for instance, acts as a filter tool, which scans and breaks down data, he adds.
“It can also scan for trends and anomalies and if you have an event that causes data to drop out, rather than skewing the data trends, you can cut chunks out and it can be automated.”
He says that via data analytics software, an operator or maintenance manager can remotely view all the process plants their company operates.
“Such a system also allows you to better understand where a plant is not producing like it should,” Todd says.
In instances where companies operate multiple facilities – and therefore have a large amount of kit – “tonnes” of data will be generated, says Michael Cushing, product marketing manager for Honeywell Process Solutions.
“However, the control systems used within the process industries can struggle to handle that data,” he says.
Next level
To combat this, an OPC UA (Unified Architecture) server can be used to take data out of a controller and bring it up to the ‘next level’ where data analysis can be performed, Cushing says.
Companies are also considering the use of ‘smart edge’ devices, such as routers and routing switches, which are designed to provide an entry point into core networks, to boost data acquisition and analysis, Cushing adds.
“Modern devices are typically all smart these days,” he says.
Darek Kominek, senior product marketing manager at MatrikonOPC, which provides equipment data connectivity software based on the OPC standard, says that through the use of Ethernet-enabled smart edge devices, data can be collected, translated and interpreted without weighing down on the control systems that run critical processes.
“Via OPC UA, everyone starts to talk the same language,” he says.
People have realised that by having open standards, industry can move forward. OPC UA is allowing major vendors to communicate within the industrial IoT and from device to device
Darek Kominek, senior product marketing manager. MatrikonOPC
Kominek also works alongside standardisation group MDIS. The group is working to streamline the Master Control Station and DCS communications on topside systems through a collective effort between subsea controls vendors, topsides specialists and oil companies.
He says OPC UA helps define a language and a grammar for how data is described for sharing between contractors and different equipment vendors.
“People have realised that by having open standards, industry can move forward. OPC UA is allowing major vendors to communicate within the industrial IoT and from device to device,” says Kominek.
Kominek also says access to Big Data via devices linked to the industrial IoT is increasingly being supported by ‘communication brokers’, which are defined by transport protocols.
“With OPC UA making use of a broker system, a lot of clients can collect information from a single server without overwhelming it because it publishes data to a broker, which can tolerate mass access,” he says.
“You can also use OPC UA to broadcast that information and those who are interested can capture it,” he adds.
Case study: malt measurement
South African Breweries (SAB), which produces lagers and soft drinks, has recently opened a new malt production facility next to its brewery in Alrode, South Africa.
Once fully operational, the plant is expected to exceed the production capabilities of its predecessor by increasing malt production from 42,000 tonnes to 150,000 tonnes per year.
The new plant features a fully automated and networked Ethernet/IP solution, implemented by Rockwell Automation.
The networked solution connects all data from the plant floor to the rest of the SAB enterprise, transforming the plant into a ‘Connected Enterprise’, which, Rockwell Automation says, accelerates industrial performance.
“By converging operations technology and information technology, we enable SAB secure access to operational, business and transactional data to improve the malting plant’s supply chain, economic and sustainable performance,” says Adrian van Wyk, business manager for power and components at Rockwell Automation’s Sub-Saharan Africa region.
“The new automated system gives SAB personnel plant-wide control, from plant floor to executive level, via a single, secure integrated Ethernet/IP network,” say van Wyk.
“By enabling secure access to actionable run-time production data, machine diagnostics and automatic fault-finding, SAB gains full visibility of the maltings plant, ultimately facilitating a faster time to market, lower total cost of ownership, improved asset utilisation and enterprise risk management for the maltings plant.”