Viewpoint: controlling drug data
9 May 2016
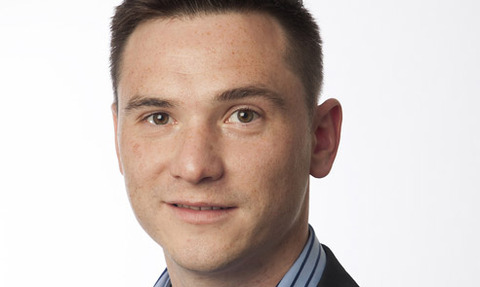
Implementing the industrial Internet of Things within the pharmaceutical sector is a big task, says COPA-DATA’s Martyn Williams.
There are clear opportunities for pharmaceutical manufacturing companies to embark on an industrial Internet of Things (IoT) journey.
The typical starting point centres on condition monitoring, predictive maintenance and analytics, but the true value will be different for each company, creating opportunities for new business models and services revenues.
Yet none of this is possible unless you can connect to existing and legacy plant systems across multiple platforms, and then using the information gathered in either an on-site or cloud-based solution.
Manufacturers can reap the rewards of real time data capture, increased visibility and the generation of reliable production data
The next step is to analyse the collected data and employ it to deliver business benefits. With the cost of cloud storage and computing lowering every day, this has become a very cost-effective solution.
The already-established trend of an increased number of sensors on industrial equipment has also meant manufacturers can reap the rewards of real time data capture, increased visibility and the generation of reliable production data.
Better communication
However, for the industrial IoT to succeed in the pharmaceutical manufacturing sector, industrial equipment from a variety of manufacturers must be able to connect to high level automation systems or devices that can access back-end databases or cloud services.
Typically, this is achieved through connected control devices, such as programmable logic controllers (PLCs).
Yet despite the adoption of automation in recent years, there are still many legacy systems in operation that fall short and even some original equipment manufacturers (OEMs) that do not support open standards in their products and solutions.
Some existing systems may only communicate locally, without networking or over non-supportable communications protocols, while in some cases the visualisation of machines has been developed in propriety software locked by the developer.
Without replacing propriety applications with open and independent automation software, the machines and human– machine interfaces (HMIs) will require re-engineering. To fix this incompatibility, manufacturers should expect increased costs for the re-engineering of systems integration.
By using open automation software compatible with a wide range of communication protocols, pharmaceutical manufacturers can ensure the transition to the industrial IoT is as seamless as possible.
Undoubtedly, data collected from industrial equipment is sensitive and should therefore be protected from unauthorised access
Meanwhile, another reoccurring challenge comes in the form of Big Data.
For IoT-enabled facilities, the ever-increasing amount of data can be a real dilemma. While an increase in accuracy and more detailed production data is, without doubt, a benefit for organisations, the abundance of information means manufacturers require a re-think of data storage, archiving and analytics.
In these instances, the obvious solution would be to migrate to off-site storage or cloud computing.
However, there remains some anxiety among pharmaceutical and medical manufacturers with regards to the idea of storing production data outside the factory walls.
Undoubtedly, data collected from industrial equipment is sensitive and should therefore be protected from unauthorised access.
However, companies can keep critical information on premise and push raw data to a cloud storage solution – the data only holds value when the two parts are combined.
This hybrid solution meets both needs, making an organisation less vulnerable to cyber-attacks, while maintaining connectivity.
- Martyn Williams is managing director of industrial software specialist COPA-DATA UK.