Why pump sizing matters
24 May 2016
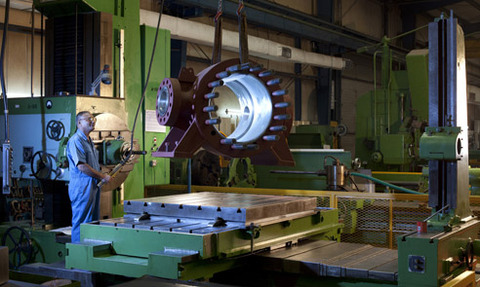
Correct pump specification is critical within the process industries. Get it wrong and the costs can be staggering. Dermot Martin and John McKenna investigate the issues associated with oversizing and undersizing pumps.
The cost of oversized, overpowered pumps can be counted in billions rather than millions. So why is it such an intractable problem?
Process parameters change over time and the fact that a pump may be oversized – and incurring extra costs – may not become apparent until a change has been implemented.
David Brown, managing director at pumping equipment manufacturer Börger UK, says the main barrier to tackling the issue of pump oversizing is a lack of understanding by some engineers. In particular, this concerns the recent development of materials and technologies that can lead to improved performance, Brown says.
“Engineers can be forgiven to some extent because normally their brief is to provide a process solution driven by a financial imperative or output improvement. The goal is to deliver more bang for the customer’s buck.”
The cost of oversized, overpowered pumps can be counted in billions rather than millions
“Where they let themselves down is in failing to apply a safety or growth margin into the equation. The pump manufacturer can only work with the information supplied. That’s why they need as much detail about the process as possible, mixed in with a level of trust,” he adds.
So how does pump oversizing occur?
It usually comes down to a lack of understanding about the precise relationship of the pump and the process system. It may be the desire to build in future-proofing for process expansion relative to the original system.
The growth of a chain of three or four contractors linked to pump design can complicate the selection process and can become a problem, suggests Ralph Kohn, rotating equipment engineer at engineering solutions business Weir Group.
Speaking up
“Each contractor will usually add their own margin of design error. This can result in three or four margins of error at 5% added to the original specification,” Kohn says.
“By the time the pump manufacturer receives the order, the perceived capacity may easily have grown by as much as 20%. Suppliers need to talk to the customer at a system level.”
According to Kohn, it is often tough for suppliers to find out what is really required in a given situation.
“Many end users will employ a ‘tier 1’ contractor to manage the entire project, or for larger projects split the work between two or more ‘tier 1’ suppliers, who in turn will bring in a layer of ‘tier 2’ consultants or subsystem designers. Soon the pump supplier finds himself dealing with third-hand specifications,” he says.
By the time the pump manufacturer receives the order, the perceived capacity may easily have grown by as much as 20%
Ralph Kohn, rotating equipment engineer, Weir Group
Clearly, the end-user and the supplier need to be singing from the same song sheet.
Technology can help address some of the problems. A good example is the use of a variable speed drive in the initial design stage.
“If an oversized pump is selected because a second process stream is likely to be brought in two or three years later, a variable speed driver could work,” Kohn suggests.
“Another option is the temporary de-rating of the final design or even use of multiple small-frame sized pumps,” he adds.
Age concern
In the majority of engineering sectors a 25-year span is used to estimate full life costs. However, there are pumps in UK power stations that have been operating since the 1970s.
A 25-year life can easily become a 40 or 50-year life model — with all the implications for efficiency and power and maintenance costs.
Brown says that up to a third of the pumps in all sectors are incorrectly specified and the vast majority of these are oversized.
“The best practice is to ‘weight-ratio’ your decision to include the initial purchase price as only a small percentage of the final decision. Technical specifications, compliance efficiency, ease of maintenance and spare part costs are the parameters that really matter,” Brown says.
“The big problem is that many contracts are won and lost on initial cost analysis. The accountants then think that value for money has been achieved.”
A third of the pumps in all sectors are incorrectly specified and the vast majority of these are oversized
Quality training and advice can also help.
Pump manufacturers will typically run training courses and will encourage visits from potential customers. It’s worth making those visits at the design phase.
Kohn says incorrect matching of pumps and systems is a real and measurable cost.
“When it comes to buying a pair of shoes, yes, you can walk into a supermarket and grab a pair off the shelf, but we all know the likelihood is they will wear out quickly. A quality pair of brogues will last years before they wear out,” Kohn says.
Likewise, time spent researching pump kit will be time well spent.
Critical issue
Correctly determining the size of a pump is critical to both the efficiency of a pumping system and to ensure a healthy life span for all of its components.
When looking at centrifugal pumps, an inefficient system is typically one that is oversized. As highlighted above, this oversizing — which is normally caused by cautious engineers building in levels of contingency to the system’s capacity — means, at best, a pump will be inefficient and fail to hit its Best Efficiency Point (BEP).
At its worst, oversizing of centrifugal pumps in, for example, a ring main system can lead to an increase in the product temperature, cavitation/NPSH issues, premature bearing failures, vibration, low efficiencies and much greater power consumption.
Correctly determining the size of a pump is critical to the efficiency of a pumping system
However, for progressive cavity (PC) pumps, the opposite is true.
“For progressive cavity pumps the worst effect of oversizing is low efficiency,” says Netzsch technical sales engineer Nick Jones.
“It’s unlikely to do the pump any harm. However, with progressive cavity pumps you have working parts in contact with each other, and when you run the pump faster you get a higher rubbing velocity between rotor and stator. This increases the wear rate and becomes more significant if the product is non-lubricating or contains abrasives.”
Gauging strain
The big danger for PC pumps is undersizing, due to the strain that is put on the pump and its components as it has to work harder and faster.
“Undersizing a progressive cavity pump leads to more problems than oversizing because the volumetric flow is determined by the cavity size, meaning that a smaller pump has to run more quickly to generate the required flow rate, leading to higher wear,” says Seepex Northern Area manager Tim Kaye.
“Also, the higher running speeds of undersized progressive cavity pumps may reduce the suction capabilities, particularly with high viscosity products, and in extreme cases lead to cavitation with all of its associated problems.”
While those designing pumping systems always seek to avoid undersizing PC pumps, just how dangerous undersizing can be depends largely on the type of material being pumped, says Jones.
“It depends an awful lot on what you are pumping,” he says.
Just how dangerous undersizing can be depends largely on the type of material being pumped
“If you are pumping something that is lubricating and contains no abrasives, then you would be happy to run the pump much nearer the top of its speed and pressure ratings.”
However, PC pumps are often used in applications where the material is very far from being “nice and slippy”, Jones says.
AD concern
Two common industrial applications for PC pumps are the pumping of sewage sludges at wastewater treatment plants, and the pumping of biological material in Anaerobic Digestion (AD) energy-from-waste power plants.
The number of AD plants in the UK has risen dramatically in recent years, and so too have the number of pump failures experienced at these plants.
Speaking at the Biogas and AD industry’s annual UK gathering in Birmingham in 2014, Landia UK & Ireland sales manager Paul Davies accused AD plant owners of “running their pumps into the ground”, saying that the demands placed on systems by increasing amounts of improperly shredded food waste and contaminants in domestic green bin waste, combined with poor maintenance accessibility, meant there was a high risk of system failures.
“AD downtime isn’t something you want,” he said at the time. “Lost revenue can amount to thousands of pounds per day and a problem with fulfilling your contract to the energy provider.”
We have seen pumps that are lasting just days or even hours because the product is so very aggressive
Nick Jones, technical sales engineer, Netzsch
Jones says that while he believes the situation is now improving, “there has been considerable undersizing of pumps in the past, because people have failed to understand how much the pump’s life can be shortened by pumping hard in abrasive duty”.
“In the biogas industry there is a lot of unwanted debris like glass. We have seen pumps that are lasting just days or even hours because the product is so very aggressive,” he adds.
Sizing-up success
The key to success in specifying PC pumps for AD plants, says Jones, is to take into account the nature of the material that may be passing through these pumps.
“A key factor with specifying progressive cavity pumps is the size of the cavities it forms in operation,” says Jones.
In general, the size of the cavity is directly related to the pumps displacement so larger capacity pumps are able to handle larger solids.
“If you are pumping something with solids, you need to consider the likely solids sizes and take this into account. If you make a model selection based on flow alone you may end up with a pump with cavities too small to pass these solids, leaving it prone to blockage and excessive wear.” The solution, says Jones, is to select a larger pump capable of handling the size of solids that will pass through, and then run it at a slower speed to give the desired capacity.
This deliberate “oversizing” can bring significant benefits, not only in terms of avoiding pump failure, but also by extending the life of the pump, says Kaye.