Maintenance software: the critical path for asset care
15 Aug 2016 by Louisa Hearn
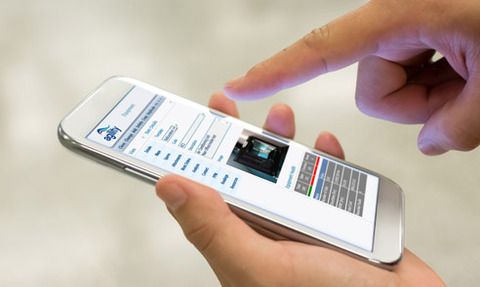
Maintenance software is plugging into the Internet of Things to help operators identify key priorities, writes Louisa Hearn.
There is nothing quite as certain as change in the modern process plant. But as ageing equipment is replaced or upgraded, how do operators monitor the knock-on effects of this on other areas of the plant?
Making sense of the interconnections between key pieces of equipment and other assets is the primary business of computerised maintenance and asset management systems (CMMS).
A deeper level of visibility is a critical feature of CMMS says David Hipkin, managing director of Softsols.
“We are seeing many companies now determining which are their most critical assets,” he says.
Only a year ago the Internet of Things seemed mostly pie in sky and hype, but now it is reality
David Hipkin, managing director of Softsols
“This demands an understanding of the asset base and knowing which are safety [critical], and having an appropriate safety and maintenance regime for that category of assets.”
Automation and connectivity are also becoming increasingly important, he adds, as companies look to make use of the masses of new data being generated.
Now, the emergence of the Internet of Things (IoT) is adding a completely new layer to the flow of information to and from asset and maintenance management systems.
“Only a year ago the Internet of Things seemed mostly pie in sky and hype, but now it is reality,” says Hipkin.
The ability to proactively monitor and home in on intelligence about a much wider range of assets offers a compelling proposition.
“If you can get information from devices into the enterprise asset system, then you can automatically see where you have failures,” he says.
Keeping track
The company’s CMMS Agility software is a combined asset database and work management solution. He says Softsols is focusing in on the drive for people to want more intelligence in terms of how to present data between assets.
“We’ve now got plant diagrams in our system that can be used to navigate around an asset, and when something is wrong, feed this back visually.”
A common starting point is to identify key pieces of equipment and fit them with smart sensors, connected to a cloud-based IoT platform that will monitor conditions such as temperature or pressure.
You might also want to monitor whether a safety guard has been opened or closed, says Hipkin. “There are some very affordable retrofit devices which you can fit to a safety guard and the system will keep a visual track on it.”
There is also demand for more mobility for the staff tasked with inspecting or replacing equipment. “This can involve gathering data and taking photos. They can do an awful lot more with mobile technology by capturing data at source and flagging it up there and then if there is an issue.
We’ve now got plant diagrams in our system that can be used to navigate around an asset, and when something is wrong, feed this back visually
This also eases the workflow through the plant “instead of handing someone a wad of paperwork”, says Hipkin.
“And because your assets will, in essence, be able to talk to each other and communicate data, this means that you can understand cause, effects, faults and performance on a much wider and more detailed scale.”
Roger Cooke, business development manager for Shire Systems, says plant operators are increasingly looking to capture information to help them achieve maximum productivity.
“Of course the golden target is 100%,” he says. “When the processes and procedures within maintenance systems are measured, this can be used to improve the bottom line of the business. The question is what do operators want to know and what do they want to measure?”
To solve this, many are starting to look at key performance indicators (KPIs), says Cooke. To this end, the company has built web interfaces between its Pirana CMMS system for smart devices and PLCs, as well as enterprise resource planning (ERP) systems.
“We can send data to external devices and systems but equally data can be provided to us to prompt action within our system,” Cooke says.
Face-time
Those devices could be part of the IoT because the system interfaces can also act as web services for meter readings and condition-based elements.
“We are well set for the IoT because one of the key issues is presenting data for input or output of systems – such as working into ERP systems to tell it which parts we need.
“We can take that data into the maintenance system to be a central point of access. That interface can occur where a customer wants to have it,” says Cooke.
It could be used by devices such as a PLC providing meter readings, or for monitoring equipment conditions and parts usage.
“Our system can output data into a predetermined format, as well as bringing data back...to ensure it has been properly validated, which might then generate a work order,” says Cooke.
The cloud is also shifting the goal posts as more businesses seek to link their asset improvement plans to the strategic long-term objectives, says Colin Beaney, global industry director for energy and utilities at maintenance and asset software supplier IFS.
He says remote management of assets is a key for tasks such as “fault-finding underground or working in a high temperature”.
He also sees a future where drones and augmented reality glasses could be used for an initial evaluation. “The drone would likely communicate through the cloud and experienced technicians stationed remotely could diagnose and lead activities during the repair.”
Mobile maintenance
One of the biggest advantages of choosing a mobile-enabled CMMS is the portability, says Mapcon Technologies.
It means workers can carry a smartphone or tablet to the floor with them, instead of having to go back to a PC to look up information.
US-based Conestoga Energy adopted Mapcon’s mobile CMMS solution a few years ago, enabling significant change within its ethanol plant.
It says inventory cycle counts have become easier because workers can either enter data manually while on the floor, or scan the parts individually, with the addition of a barcoding module.
Maintenance engineers can also run reports, approve purchase orders, and create work requests with photo attachments, directly from the floor.
Mobile notifications are also saving time, because staff can receive an alert on their smart phones when a work order is dispatched.
“If I need a report during a meeting that I didn’t print off beforehand, I can just bring it up on my iPad,” says Allen Bryant, Conestoga’s maintenance manager.
Bryant says he is also able to run reports from his tablet when he isn’t at the plant.
Purchase orders and mobile notifications also appear on his phone, so when a critical part needs to be ordered, he can action this right away.