Networking: the cost of bad communication
10 Oct 2016 by Rob Smith
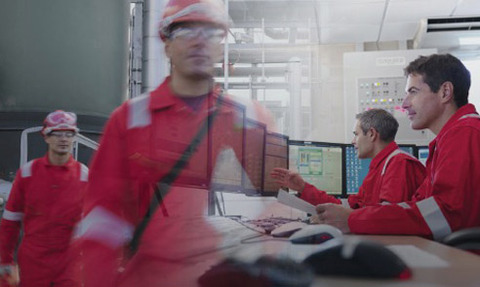
Industry is fighting against a tide of inadequate networking systems, while also attempting to unify communication standards, writes Robert Smith.
Networking and communication infrastructure is seen as the nervous system that connects a process plant together.
So if a plant’s nervous system isn’t up to scratch or isn’t operating effectively, the plant loses the ability to communicate.
Ultimately, this loss of communication will translate into unplanned downtime and loss of production – something that operators try to avoid at all costs.
But despite these networks being so vital, operators have been known to take risks and install inadequate systems, says Ray Lock, network technology director at data communications company Westermo.
Price is right
One of the major issues is that quality networking and communication infrastructure comes at a price. This is coupled with the fact that much cheaper technology is readily available.
“Clearly, though, you get what you pay for and cheaper kit tends to be far more inferior than products from the likes of Yokogawa or Honeywell,” says Lock.
He says networking and communication infrastructure from more established industry players is built to last and designed to operate in an industrial environment.
However, there was a paradigm shift in the industry when IP was introduced, which allowed a lot of companies to be able to use enterprise equipment, such as switches from the likes of Cisco or Dell, Lock says.
“Unfortunately, this type of equipment doesn’t tend to last long when used for process industry operations.”
He adds that cost-cutting exercises have brought about a “race to the bottom” attitude – even though the majority of vendors understand the need for reliable networks.
Companies that are serious about having a decent communications network should always select products from manufacturers that are committed to things like working with a number of maintenance releases each year
Ray Lock, network technology director at Westermo
Therefore, product testing is a major part of ensuring high-end kit is as robust as the manufacturers say it is.
At the quality end of the networking and communication infrastructure spectrum, production units are sent to a variety of test facilities and scrutinised by third-party companies.
This is something Westermo does, Lock says. More robust products will also typically feature maintenance software pathways, he adds.
“Companies that are serious about having a decent communications network should always select products from manufacturers that are committed to things like working with a number of maintenance releases each year,” he says.
“These releases could be anything from new features to patches for their kit.”
Lock says cheaper products, which don’t have security as standard, could cause any number of unnecessary maintenance issues for a company.
“In-built security cultures, which are in place to help a company stay on top of cyber threats, go out the window if you buy cheap.”
Quality required
Part of Lock’s job is to advise against such installations, but he says regardless of how much you hammer the point home, there’s always a way for inadequate kit to make its way into a plant.
He says managers at the top of a company will often specify the best kit, but by the time these specifications have made their way down to the systems integrators, there has been a squeeze on price.
“They need to be cost competitive…so if they buy the equipment the plant operator originally asked for, profit margins are reduced. Naturally they look for areas to save.”
However, he says the best contract managers will give clear instructions and make sure their systems integrators stick to them. “Good contract managers will enforce the rules from their sub-contractors down to the system integrators. If those guys have a problem with it, a good contract management chain will have a feedback path, allowing for discussion of issues.”
Good contract managers will enforce the rules from their sub-contractors down to the system integrators. If those guys have a problem with it, a good contract management chain will have a feedback path, allowing for discussion of issues
Ray Lock, network technology director at Westermo
Fortunately, Lock says the above issues are increasingly becoming a thing of the past, particularly as language becomes standardised.
Open standards such as OPC UA (Unified Architecture) are creating a single voice with which a variety of industrial equipment can communicate.
OPC UA-enabled equipment, which increasingly exists in an industrial Internet of Things (IIoT) environment, creates communication and data flow that is not only upwards, but also among machine-to-machine (M2M) devices or outside and into the Cloud, says Darek Kominek, senior product marketing manager at MatrikonOPC, which provides equipment data connectivity software based on the OPC standard.
According to Kominek, companies are now more aware that products certified under OPC UA are more resilient to threats.
“This is because the standard is designed around security. It has even been tested by BSI – the IT security branch of the German government, which said OPC UA was robust enough to handle their ‘Industry 4.0’ requirements.” This is a strong statement for an entire country to make, and one that is likely to pique the interest of the process industries, Kominek suggests.
He adds that without OPC UA, it is likely products will be considered less competitive in the marketplace.
As with anything new, it can take a long time for the right messages to penetrate across the market. There is a lot of education that is still needed so that people become aware of what is available or what approach to take for their systems
Darek Kominek, senior product marketing manager at MatrikonOPC
So true is this, Microsoft now lists OPC UA as its recommended method for connecting industrial systems, says Kominek.
“They have put their weight behind this communication standard and have said OPC UA is their preferred method of communicating and shaping data before it goes off into the Cloud.”
Kominek says that because OPC UA/IIoT integration is aligning, it is becoming easier for the market to digest and have confidence in the approach. However, he concedes there is still a way to go in educating enough people about the benefits and options that exist within OPC UA/IIoT integration.
“As with anything new, it can take a long time for the right messages to penetrate across the market. There is a lot of education that is still needed so that people become aware of what is available or what approach to take for their systems.”
Changing of the guard
Proprietary networks and communication protocols are one of the recent casualties of fluid communication in the factory.
“They have been replaced in favour of the uninhibited free flow of data,” says Jonathan Wilkins, marketing director of automation spares supplier EU Automation.
And despite proprietary communication protocols previously being hailed for their safety in comparison to their standard and open counterparts, plant managers have been screaming out for standardisation, Wilkins adds.
“This was fuelled by the desire for a reduced total cost of ownership, more manufacturing productivity and synchronisation of the entire supply chain. In short, the manufacturing masses wanted in on the Internet of Things (IoT).”
He says that plant managers have a very good reason for this.
“The IoT has made the modern plant a hive of automated data transfer, facilitating lean manufacturing, quicker decision-making and smart raw data analysis,” Wilkins explains.
Furthermore, he says the concerns regarding safety with standard protocols have been counteracted by businesses taking the proper precautions to protect assets and infrastructure.
“Standard communication protocols like OPC UA (Unified Architecture) give compatible devices function blocks that are able to communicate over industry standard Ethernet using common data models.”
Communication is also no longer limited to the factory floor, says Wilkins, which adds another nail to the proprietary network coffin.
OPC UA transcends the automation pyramid and allows PCs on the enterprise level to transfer information with sensor level devices, he says.
“We therefore have to ask whether proprietary protocols and networks will ever make a resurgence, or have they had their day? We know which side we’re rooting for
Readers' Comments
There are no comments on this article, leave a comment below to have your say
Have Your Say
The comments have closed for this article