Chemical challenge – UK industry seeks fresh industrial strategy
8 Nov 2016
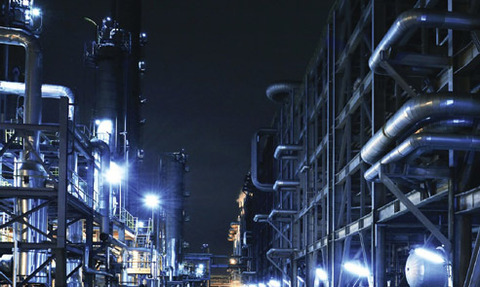
Manufacturers are fighting for change in an already volatile industry, writes Robert Smith.
The UK manufacturing sector is experiencing something of a high at the moment.
Last month the Markit/CIPS purchasing managers’ index (PMI) indicated the sector had grown from 53.4 in August to 55.4 in September.
Any figure above 50 is considered a sign of expansion. Lee Hopley, chief economist at manufacturers’ organisation EEF, says: “The expectation-busting surge in manufacturing activity points to conditions across industry being considerably better than business as usual, with expansion in output and new orders in all industry segments boding well for growth in the second half of this year.”
She says that, while UK exporters have the added boost from the weaker exchange rate, it’s the prospect of brighter demand that provides confidence in growth holding up.
High ratings
Elsewhere, UK manufacturing entered the ‘world top 10’ in September – making it the ninth largest industrial nation according to research by EEF and banking firm Santander.
Regionally, London and the South East dominate, producing output of almost £28 billion, while the North West creates £23.7 billion and the West and East Midlands make £16.4 billion each.
Commenting on the research, Charles Garfit, head of manufacturing at Santander Corporate & Commercial, says it is interesting to see that there has been growth in the non-traditional sectors and regions which demonstrates the increasing importance of manufacturing across the country.
In total the UK has an estimated manufacturing output worth $247 billion (£188bn). Of that figure, pharmaceutical and chemical manufacturing accounts for 14%.
Currently, many countries perform their own testing rather than use data from other countries. This produces unnecessary duplication, where the money would be better spent on combined testing and research
Trish Kerin, director of the IChemE Safety Centre
However, the data does nothing to explain how difficult it can be to get pharmaceutical and chemical products to market.
For instance, before a chemical is mass-produced and exported around the world, its manufacturers must first understand the inherent risks associated with that product.
Trish Kerin, director of the Institution of Chemical Engineering (IChemE) Safety Centre, says this approach incorporates research and testing to ensure that manufacturers understand the impact these substances may have either from their use or misuse.
“Examples here include the introduction of asbestos, nanoparticles or persistent organic pollutants (POPs),” Kerin says. Though products like asbestos and POPs have a range of positive benefits, she says there are significant hazards that need to be managed.
“In some instances this is by elimination, either because their negatives far outweigh their positives, or because there are safety alternatives.”
In the know
Kerin says there is also a responsibility to constantly gather data on the threats posed by chemicals, again citing asbestos as a good example. “The risk of asbestosis has not changed over time, but our knowledge of how it forms has evolved since asbestos first entered the market.”
This is a major reason why industry must appropriately test and research new products and formulations to ensure there is an adequate understanding of the consequences of use and foreseeable misuse, Kerin says.
“We also need to be better at sharing this information across countries. Currently, many countries perform their own testing rather than use data from other countries. This produces unnecessary duplication, where the money would be better spent on combined testing and research.”
Efficiency focus
Once a product is at the stage where it can be mass-produced, Stan Higgins, chief executive officer of the North East Process Industry Cluster (NEPIC), says the major threat to industry comes in the form of the gradual loss of efficiency and increasing costs. He says this is due to the lack of focus on the needs of these foundation industries.
“Around the world, others are developing smart industrialisation policies to maximise integration and materials symbiosis to increase efficiency and reduce costs, while at the same time other countries are making best use of their own natural resources,” Higgins says.
“By focusing on these big ideas – that need infrastructure support from the Government – we can bring about a vast improvement to our balance of payments and ensure that UK industry is highly sustainable into the future.”
He says the government needs to understand that the chemical industry and its downstreamdependent industries would be more secure if rebased on UK raw materials.
“This is the way in which huge potential risks for existing and future investments can be removed.”
Around the world, others are developing smart industrialisation policies to maximise integration and materials symbiosis to increase efficiency and reduce costs, while at the same time other countries are making best use of their own natural resources
Stan Higgins, chief executive officer, North East Process Industry Cluster
Higgins says the chemical industry could have access to secure raw materials as well as better political and economic control of its energy costs if it were to make use of the UK’s abundant coal reserves, which he says amounts to 10,000 years’ worth of supply.
These reserves should be accessed with clean technologies, he advises. “Many of these technologies are already available to implement for extracting gas from deep underground coal fields, capturing carbon dioxide (CO2) emissions for storage, or better still, reuse in the many emerging chemistries that convert CO2 to plastics, battery electrolytes and fuels.”
He also points out that during July, scientists from the Argonne National Laboratory and the University of Illinois demonstrated the photosynthesis of CO2 – in photovoltaic-like cells – to syngas.
“[It’s] a result which is almost the ‘Holy Grail’ for the chemical industry.”
Industrial strategy
However, in the immediate future, the UK chemical industry must seek to benefit from a new industrial strategy says Felix O’Hare, a colleague of Higgins’ and project manager at NEPIC.
In canvassing opinion from NEPIC’s members, O’Hare says asset-intensive industries need a consistent medium to long-term strategy. This would encourage rejuvenation and growth in these sectors, O’Hare says.
He argues that any future UK industrial strategy must support and underpin the growth of UK industry, aiming to ensure it can become sustainable and globally competitive in the longer term.
Calling for the need for more joined-up thinking, O’Hare says: “What is required is an integrated strategy that links the underlying materials-producing sectors, such as chemicals and steel, to the downstream sectors, including automotive, aerospace, personal care, agrochemicals and food.”
Failure to work in this way has impacted the sector before, he says – citing the loss of the country’s only ethylene oxide plant on Teesside in 2009 as an obvious example.
It was a move that resulted in costs of more than £5 billion, O’Hare adds. “The powers-that-be could not understand how this could happen and did nothing to help,” he said.
What is required is an integrated strategy that links the underlying materials-producing sectors, such as chemicals and steel, to the downstream sectors
Felix O’Hare, project manager at NEPIC
“After all, the unit only employed 70 people. Six months later they came back to us and apologised, as they saw that within months, almost every drop of surfactant that the country uses was suddenly being imported and several downstream factories moved offshore as a result.”
To avoid further problems, he says modern industrial strategy must focus on: aligning itself with a low-carbon future; optimising the benefits of key manufacturing clusters; ensuring multiple industries are better connected; guaranteeing the UK is considered as a destination for inward investment, and focusing on skills development.
“The strategy needs to be owned in partnership by government industry trade associations and Industry Cluster bodies, and its implementation supported financially with appropriate programmes and infrastructure projects,” O’Hare says.
“What’s more, the voice of individual companies must not dominate in its implementation.”