Case study: Xylem brings pumping solutions to beermaker Brewdog
25 Jul 2017
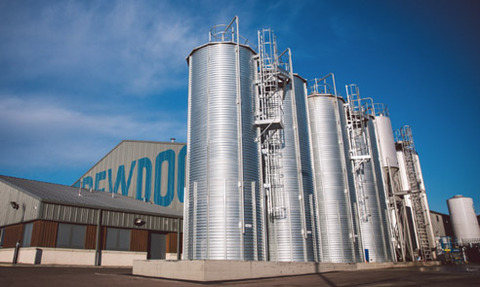
Craft brewing requires a revolutionary approach to ensure consistency – which is why this Scots brewer turned to Xylem for a pumping solution.
In an environment such as the brewing industry, high-operating temperatures and fibrous hop sludge play havoc with pump equipment if it’s not specified correctly.
So, when Scottish craft brewer Brewdog was looking for a robust pump solution, they turned to Filpumps and Xylem for the answer.
For the brewery team in Ellon, Aberdeenshire, there were two key issues with their existing pump system, resulting in increased costs and downtime needing a quick resolution.
In the first instance, the fibrous quality of hop sludge was threatening to cause build-ups and blockages at the base of the conventional, flatbottomed, packaged pump station – creating delays to the brewing cycle with plant downtime and expensive tankering costs.
Our close working relationship with the team at Filpumps meant that we could find the very best solution for Brewdog
Alan Black, field sales engineer, Xylem
Secondly, where the effects of high temperature on pumps and float switches had not been considered during specification provided for the existing system, there was a risk to its efficient and effective operation.
Xylem, working in partnership with local distributor Filpumps, recommended the use of their ‘warm liquid’ N-impeller pump range.
Alan Black, field sales engineer at Xylem, says: “Our close working relationship with the team at Filpumps meant that we could find the very best solution for Brewdog.
“Marc Elrick and Paul Brennan at Filpumps played a key role in specifying the ‘Flygt Experior’ pump station, featuring the Flygt N 3153 warm liquid pump and a control panel complete with SmartRun VSD pump controller and telemetry.”
Riding high
Thanks to the Flygt N 3153’s high temperature feature, along with the self-cleaning technology of the N-impeller design, it proved the solution for the transfer of the problematic trade effluent at the end of the brewing cycle.
Featuring reverse run and sump clean/snore settings, the self-cleaning SmartRun controller helps to maintain the high-efficiency of the pump, while keeping the production processes moving. This allows customers to reduce energy costs and unplanned service calls, says the company.
The pump is equipped with a Class H motor stator with a design temperature of 180ºC max, compared to traditional Class F designs of 155ºC. Motor losses are also concentrated at the surface of the stator rather than the rotor, making it easier to transfer the heat into the pumped media.
It is testament to the team’s knowledge and understanding of this kind of application and the success of our products
In addition to the pump protection features, the Experior SmartRun package provides the benefits of variable speed pumping, and is designed to achieve energy savings and maximum cleaning within pumping stations.
Flygt SmartRun’s variable speed controls are also a good match for Flygt N-pumps, while delivering reduced total expenditure for the end user.
Brewdog was so impressed by the success of the Flygt pumps, that Xylem and Filpumps were later invited to advise on the phase 3 expansion, resulting in a further order for a Flygt TOPS packaged pump station, Flygt Experior pumps and SmartRun technology.
Black adds: “It is testament to the team’s knowledge and understanding of this kind of application and the success of our products.”