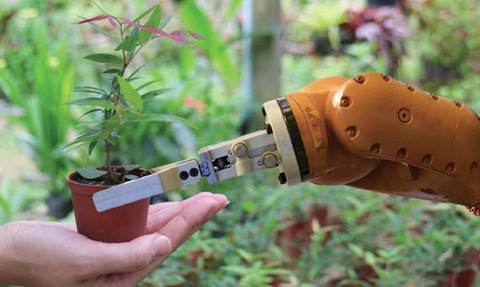
Once seen as slow moving and traditional, the food and drink sector is in its most dynamic period for decades. Legislative changes, skills shortages and, as ever, Brexit are all contributing to new approaches to process and working culture, reports Brian Attwood.
Customs, labour and safety have been identified by the Food and Drink Federation as the trio of factors that will exert most impact on activities within the sector over the next decade.
The journey of ingredients or product to and from the UK’s biggest trading partner – continental Europe – will be subject to customs controls of some sort, for which the bedding-in process will only increase the variables influencing delivery.
Combine the scenario of a workforce that is inadequate in quantitative and qualitative terms with the demands of operating in an environment that requires a more agile response to what could be fast-changing regulatory and export/import regimes. An obvious potential casualty is likely to be food safety levels, which would in turn affect sales.
When businesses have the data they need, acquired directly from the customers, they can make better informed decisions
Roger Haenni, co-founder and CEO, Datum
Yet the recent 2 Sisters Food Group scandal, which involved both tampering with poultry slaughter dates and the return of meat to the production line after falling to the floor, is a reminder that there is already substantial cause for concern.
Jason Chester, global strategic account manager for Infinity QS Europe, which specialises in data-driven manufacturing intelligence, comments: “The findings from the investigation into 2 Sisters highlight a much wider concern as to why industries, with potentially high goods-safety issues, such as food manufacturing and particularly poultry, are at risk of tampering, with staff easily able to change records of fact.”
Leading retailers may pride themselves on the stringency of their own processes and the efficiency of their automated data capture, guaranteeing traceability and auditing operations. They cannot assume the same at other points of the supply chain, says Chester.
“Understandably, incidents of this nature will raise serious questions of trust between supermarket, supplier and the consumer. In practice, this might cause supermarkets to take a much more front-footed approach to see how produce is handled, stored and processed.”
The Budget and the government’s recently unveiled Industrial Strategy offer evidence of a commitment to addressing such issues; the doubt is whether the multi-million pounds-worth of investment now promised comprise a game-changing amount.
Positive thinking
Yet a more optimistic hypothesis was advanced by Sky News economics editor Ed Conway in a recent Times article late last year.
Its two most pertinent observations were, firstly, that the EU regulations, to which Britain currently adheres, function as a recognised gold standard for much of the world. Is it possible then that customs disruption at least may prove to be less troublesome than expected?
Secondly and crucially, it is plausible, argued Conway, that new manufacturing approaches could ‘reshore’ production and reduce supply chains in favour of more localised entities.
The same thesis is explored more fully by Universal Robots in its recent White Paper Cobots as a catalyst for reshoring which states: “The ‘big picture’ significance of reshoring lies in bringing the points of production and consumption closer together, reducing the massive logistics chains involved in a globalised infrastructure, and reducing the environmental impacts that result from these.”
Steve Lindsey, CEO and founder of Lontra [pictured above], concurs. His company is collaborating with food and drink firms to replace traditional pneumatic conveying systems and recently received Horizon 2020 funding to bring its energy saving blade compressor to new markets.
“It is a very real prospect that the improvements in efficiency and reduced downtime brought by innovations such as the Lontra Blade Compressor, can make UK companies more globally competitive. This enables on-shoring and local production, improving UK productivity and potentially allowing a complete re-evaluation of current supply chain,” agrees Lindsey.
“If net migration continues to fall, the high reliance on EU labour will need to be addressed. Improvements in productivity through innovations will be essential to prevent costs rising and hence UK standards of living stagnating.
“Food safety is one of many pressures driving new technology adoption in the marketplace. Successful companies must continue to develop and innovate to maintain and grow their market position.”
Old problems, new tech
Innovative approaches have enabled firms to overcome longstanding issues. Fanuc UK’s M20iB/25C robot [pictured below] has key features for cleanroom environments.
Cables and motors enclosed in the body allow wash-downs with cleaning agents, white epoxy paint that meets FDA standard 21CFR 175.300 reveals dirt, while axes use food-grade grease and bolted user taps to prevent the accumulation of water in tap holes.
Mettler Toledo, meanwhile, has tackled the so-called ‘product effect’ on product inspection systems, whereby the electrical signal generated by foods with a high moisture, salt content or packaged in metallised film, reduces detection sensitivities in meat applications to a level far below those for dry food.
Its Profile Advantage metal detector’s use of algorithms effects a 50% improvement in detection sensitivity levels, irrespective of packaging material in challenging applications such as wet, warm or chilled food, says production inspection specialist Daniela Verhaeg.
Meat and poultry producers can see false rejects rates associated with product effect when trying to detect the smallest metal contaminants reduced by up to 95%.
Additionally, the company’s X39, developed for free flow, frozen formed food applications, can conduct ten integrity checks at 1,800 pieces a minute – an industry first, asserts Verhaeg.
Product inspection systems can also integrate with other equipment in order to add value, improve productivity and improve product quality. For example, Mettler checkweighers are often used to monitor the weight of packaged products.
Says Verhaeg [pictured]: “They are also able to interact directly with fillers, for example, to ensure regulatory compliance in areas such as weights and measures without wasting valuable product – either through giveaway or the need to rework.”
Similarly, X-ray systems employed in checking packages for missing components or for product defects such as shape and edge faults or holes can also be used for mass measurement purposes, fill level inspection and the identification of trapped product within the seal of a package.
Used in combination, simultaneous contamination and integrity checks can significantly reduce waste, rework and downtime to deliver bottom- line savings.
Connected all the way
An increasingly joined-up approach yields benefits in terms of harnessing data and providing transparency.
Better connection between automation and the manufacturing execution provides a better oversight and insight on the production floor, allowing speedier track and trace of products. This allows faster removal of faulty items from shelves and less risk to consumers.
Those consumers too can contribute to the process – not only providing market information but enabling firms to avoid the financial and environmental pitfalls of over-production.
Decentralised data store company Datum’s work with Groking Lab, producer of the Ozmo smart water bottle, is one example.
CEO Roger Haenni explains: “When businesses have the data they need, acquired directly from the customers, they can make better informed decisions. Relying on sales and inventory reports [may result in] huge lag times and may not accurately reflect the market needs.”
Technological innovation can certainly help drive productivity by driving manufacturing efficiency, but it can also have a bigger effect in making companies more globally competitive
Steve Lindsey, CEO and founder, Lontra
Such innovation is not confined to one end of the ‘farm to fork’ spectrum. Dutch firm Connecterra’s Ida app is designed to attach to an individual cow and provide updates on peak periods for insemination, digestive disorders that affect milk output, breeding suitability and calving progress. All with the intention to reduce the unpredictability of farming and maintain a stable return on investment.
UK manufacturers’ organisation the EEF’s recent industry survey in collaboration with Santander revealed a substantial acknowledgement of the benefits of process innovation, in terms of lower production costs and higher productivity. But, as chief economist Lee Hopley acknowledged: “not all companies are moving forward at the same pace.”
Startups aside, innovation favours economies of scale. Yet the labour and skills shortage makes the challenge of digitalisation and automation less easy to evade.
In the food sector, the impact on safety and product recall provides extra incentive towards greater digital penetration, not least because there are now mechanisms that can hold supply chain partners more effectively to account.
Data integrity
Blockchain, which powered the success of Bitcoin, provides a ledger for all participating parties in a supply chain. Pooling data, with every contractual and process action stored and validated, it ensures no individual participant can misleadingly alter the information.
Among the food and beverage early adopters is the Co-op, working in collaboration with the London-based platform Provenance. Data from supplying farms and factories is combined with that for the Co-op’s retail outlets and depot and can be viewed by participants and consumers on its journey from farm to shop.
Whether Brexit heralds an era of contracting supply chains, their complexity is unlikely to reduce. Meanwhile, pressure for validation and visibility will increase, stoked by demands for safety, competitiveness and environmental responsibility. In this context, blockchain will be a game changer.
For Lontra’s Lindsey, technological innovation has a double benefit for manufacturing, where productivity has historically been the most volatile within British industry.
“Technological innovation can certainly help drive productivity by driving manufacturing efficiency, but it can also have a bigger effect in making companies more globally competitive,” he comments.
“This can help us grow large UK-based, high productivity companies from the current base of small and medium sized enterprises, which in turn will have a significant effect on the UK’s productivity as a whole.”