AODD pumps can solve pump leakage from aggressive liquids
10 Jan 2018
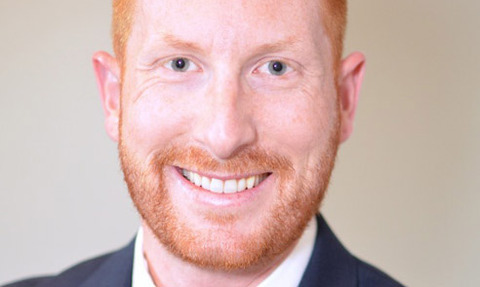
Leaky pumps create unscheduled downtime but aggressive acids and slurries can cause them to leak much faster, creating an unsafe work environment. Properly assessed, AODD pumps offer a solution explains Michael Sandlin.
Most pump designs rely on mechanical seals for chemical containment, although these are known to be prone to chemical erosion and leaking.
However, air-operated double diaphragm (AODD) chemical pumps eliminate the need for them by using bolts to secure the pump and create an effective seal.
In addition, the diaphragms move in gentle cycles to minimise turbulence and protect the liquid from shearing.
Lastly, because AODD pumps are powered by compressed air rather than electric motors, they can dry run and deadhead without the risk of burning, seizing, or harming internal components.
The crucial factors of the AODD chemical pump selection process are chemical containment capabilities, corrosion resistance, and icing prevention.
Leaking
Even some of the best AODD pumps struggle with leaks over the course of the pump’s lifespan.
Although this may seem unavoidable, costs of employee injury and wasted materials are too great to ignore.
With plastic AODD pumps, leaking is often a result of cold flow and creep, caused by high temperatures, amount of time under load, and level of torqueing stress.
Visual clues can indicate the need to replace a pump: a corroded pump exterior, leaks around the manifolds, worn internal fluid bowls, and discoloration on the floor
Plastic pumps can be damaged by continuous loads at fluctuating temperatures (‘cold flow’). As temperature increases, the effects of cold flow on a plastic AODD pump escalate, causing deformation of the pump over time, prompting components to release against compression points and leak.
‘Creep’ – total deformation of the pump beyond the immediate strain of loading – can cause significant leakage.
PTFE is one of the most chemically compatible materials for resisting corrosion but is susceptible to cold flow, as is UHMWPE – second to PTFE in terms of chemical compatibility and similarly susceptible, but at a lower rate.
Also, violent forces of operation and continuous loading can eventually loosen the AODD chemical pump’s bolts and create leak paths. End users are recommended to re-torque bolts regularly.
Some AODD pump designs require even further leak prevention steps, such as the use of reinforcing metallic plates to evenly distribute the load from the housing bolts.
A proven solution for leak prevention is a machined body reinforced with a dual force, tie-bolt design. Machined housing components are essential to provide a precision fit that will distribute the load evenly and greatly reduce leaking; components made with PTFE and UHMWPE, which are highly susceptible to creep and cold flow, are held securely by tie-bolts that are resistant to the effects of cold flow and violent forces.
Corrosion resistance
Pumps with exposed metal or wet parts composed of metal are highly vulnerable to corrosion.
Therefore, AODD chemical pumps designed with metal free exteriors will be more durable. Similarly, interior corrosion can be prevented using PTFE and UHMWPE fluid paths.
Air motor icing
Because AODD pumps are operated by compressed air, they are subject to rapid changes in temperature. One possible feature of an AODD pump for icing resistant air systems includes parallel pilot shifting valves.
This stall-free design reduces icing and maintenance needs while keeping production moving.
Several visual clues can indicate the need to replace a pump: a corroded pump exterior, leaks around the manifolds, worn internal fluid bowls, and discoloration on the floor caused by severe leakage.
Premature deterioration can be prevented by carefully selecting the best quality pump for operational needs. A dual force, tie-bolt design and precisionmachined components offer a leak-free precision fit for effective chemical containment and safe operations.
* Michael Sandlin is global product marketing manager – process division – at Graco