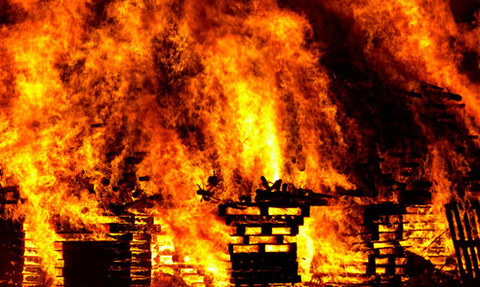
Expert advice is essential when dealing with hazardous areas and ATEX compliancy, but also taking time to train staff produces more efficient and cost-effective outcomes, learns Brian Attwood.
It is now some 15 years since the EU’s ATEX (from the French, ATmospheres EXplosibles) directives on protecting employees from explosion risks in the workplace came into effect, enforced via the Dangerous Substances and Explosive Atmospheres Regulations (DSEAR).
Yet, as one of the country’s leading experts in this field, professor Mike Bradley (director of The Wolfson Centre for Bulk Solids Handling Technology) ruefully notes, too many companies remain unaware of the demands placed upon them or lack the confidence to ensure proper enforcement.
Indeed, the problem may be getting worse: “There are situations where people have unknowingly imported an ATEX situation to their site where they don’t have any expertise whatsoever. Supermarkets, hospitals, schools – many of them are using wood pellet fuel and of course wood pellet fuel brings with it wood dust and wood dust brings with it an explosion hazard,” warns Bradley.
“The bigger risk is people not understanding the asphyxiation risk with pellet stores. If a store is sealed for some while, the pellets have used up the oxygen. Without enough oxygen to breathe, you can collapse and black out without realising. It is only a matter of time before a child crawls into one of these stores and dies.”
Within the process industries, the situation is better understood but every informed observer will recall firms who remain ignorant of ATEX.
Compliance engineer at Lorien Engineering, Emma Watson [pictured], outlines the problem: “We have come across companies that have no knowledge of ATEX or DSEAR where we needed to spend time explaining what we are doing, leading to concerns that any changes we want them to make fall on deaf ears.”
Experts, not substitutes
External expertise can be brought in to assist in ensuring all areas are compliant and nothing has been missed, says Watson. When extra measures are recommended, a ‘to-do’ list can be provided for firms that explains which areas of the process would be classified as a hazardous zone and what category it would fall into.
Advisors can suggest what equipment needs to be ATEX rated and what level this needs to be, and also provide training to staff to ensure there is a basic level of understanding of what is being carried out and what the dangers exist.
For example, she says, a company switching a silo from salt (not explosive) to cocoa powder (which needs little energy from an ignition source to explode) must reassess protection measures first.
Too often, says Robert Bussey, process safety manager at BPE, companies engage external consultants to produce a report and believe they have addressed their ‘responsibility’.
“The ATEX directive has a specific requirement for employers to train their operators and who better to identify hazards? Each company is the expert on its own processes. By having knowledgeable, well-informed operators you are empowering the workforce with their own safety.”
Bradley agrees, urging plants need someone on the inside “who will be able to embrace (ATEX/DSEAR) enough to know what they’re being told, especially if changes are being made”.
We have experienced many places where zones have been exaggerated, which can cause a high additional cost on a site. These costs come from installing ATEX-rated equipment into an area of a process where it is not needed
Emma Watson, compliance engineer at Lorien Engineering
He cites the case of a power station where a biomass conveyor in the head house was subject to substantial dust deposits. As he regularly reiterates “it’s dust on the floor that kills people in the end”, fuelling secondary explosions with sometimes devastating loss of life.
Engineers at the power station proposed to cover the conveyor in order to reduce dust in the head house. This would have created a conduit between the transfer silos and everything else, with the potential to increase the scale of any explosion. However, says Bradley, the engineers had the foresight to re-consult the Wolfson team before acting.
Elsewhere, those tasked with the responsibility in-house but lacking confidence in their grasp are often likely to over-zone, says Bradley, over-estimating the risk and, with it, the cost and protocols involved.
“We tend to apply a higher level with assessment in the UK, possibly it’s down to a lack of confidence and a tendency to over-zone. I’m not saying one should be cavalier with assessment but you’ve got to be realistic; if you over-zone then you put yourself in for a lot more expense.
“In Europe they are willing to look at areas and think ‘what’s the real likelihood?’ Yet everyone is nominally using the same rules.”
This comes down to training, says Watson, who notes that DSEAR assessments sites where operators have received training result in a much smoother, time-effective process.
“We have experienced many places where zones have been exaggerated, which can cause a high additional cost on a site. These costs come from installing ATEX-rated equipment into an area of a process where it is not needed,” she says.
By contrast, zones that have not been identified or have been underestimated can cause ignition sources to be introduced to the process.
“If staff in either of these examples had been trained with even basic knowledge of ATEX and DSEAR they would have been able to question the zones that had been presented for the processes.”
Bussey [pictured] regrets that, while there was a flurry of responses when the directives and regulations launched, “in recent years, and given the economic climate, many companies have cut back on safety training, this is often one of the early casualties during cost reduction exercises”.
However, short courses such as the Wolfson’s one-day DSEAR module are increasingly popular in-house and more effective because they can encompass management, operator and intermediate level employees.
Stepping up to the plate
While safety implications remain the priority, significant cost and efficiency gains accrue from a pro-active, informed approach outside the classroom, advise Bradley and Watson.
Many basic protocols are simple to implement and increase the safety of the site, without bringing in external expertise, advises Watson, combining cleaning and containment:
- Good housekeeping – where leaks are cleaned up immediately and rarely occur.
- Planned and preventative maintenance
- Anti-static flexible connections
- Earthing so static build-up is dissipated and does not cause an ignition source
Investment in maintaining housekeeping is extremely important, says Bradley, citing Drax power station in North Yorkshire, where thorough work ensures 10 tonnes of dust is removed from the factory floor daily. Keeping plants properly clean reduces zoning, saves cost and offers more flexibility with equipment used.
For Bussey, containment is key and there’s as strong a business as a safety case: “Material that needs to be cleaned up is potentially lost product and lost revenue. Why would you pay operators to clean up, rather than focusing on making product to sell?”
Together with good dust control, better handling and removing dust from material it can also limit the expense of over-reliance on dust extraction firms. While extraction may still be required the job will be smaller, cheaper and more effective, states Bradley.
“If you’ve got combustible material and dust people need to understand why, and if they understand why, then they’re more likely to do something about it. It isn’t just about the know-how – it’s about the know why.”