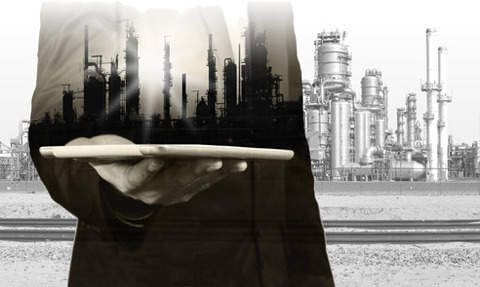
While IIoT is fast becoming a fact for some businesses, Robert Smith asks if the majority of engineering firms have yet to feel the benefit.
The Industrial Internet of Things (IIoT) will add an estimated $14.2 trillion to the global economy by 2030, according to a recent report by management consultant Accenture. To put this into perspective, today’s global economy is worth around $80 trillion in total.
The report, which outlines the opportunities and key actions at the heart of IIoT connectivity, predicts that the Internet of Things will help accelerate the reinvention of several industrial sectors, including manufacturing and energy.
Outlined in a separate report, Accenture and the World Economic Forum say the IIoT will combine the global reach of the internet with a new ability to directly control the physical world, including the machines, factories and infrastructure that define the modern landscape.
It is hard – there isn’t a silver bullet that will change everything overnight, but in five years we will be amazed with the progress that’s been made
Dan O’Brien, director of strategy at Honeywell Connected Plant
That report concludes that the IIoT “will change the basis of competition, redraw industry boundaries and create a new wave of disruptive companies, just as the current internet has given rise to Amazon, Google and Netflix”.
Connectivity is at the heart of this disruption. The number of connected devices has shot up in recent years. Market researcher Statista says that by 2025, over 75 billion IoT devices will be installed, which represents an increase from around 15 billion in 2015 and well over three times more than today. However, according to Dan O’Brien, director of strategy at Honeywell Connected Plant, hype around the IIoT “is dead”.
“A while back it was all about the hype, all about the connectivity, all about the smart devices, all about edge analytics, but I think we have [moved past that phase]. Now what excites me most, is that the IIoT is an accepted part of the normal course of business for many of our customers,” he says.
Data drive
Companies like Honeywell are using the data generated from connected devices to deliver insight to their customers and improve production processes in real time.
Elinor Price, senior product manager at Honeywell Process Solutions, says this is one of the major benefits of broader understanding and implementation of IIoT capability.
Price says that through Honeywell UOP’s Connected Performance Services tool, it can monitor and interpret information from a plant and understand how best the facility should be operating.
“And based on expertise and the models we have, you can also drill down into the root cause of issues and the insight can be used to inform people on site,” she says.
What makes the Maturity Index so useful is that every single action delivers measurable benefits and the process is traceable at all times
Paul Taylor, head of industrial products (UK) machinery safety, TÜV SÜD
Using data in this way allows Honeywell to provide assistance even down to the individual engineer level, O’Brien adds.
“Through these services, we can send push notifications to individuals, provide dashboards, and sometimes we monitor events so we can reach out and let them know we have their back.”
Unsurprisingly, much of this capability has been made possible because of advances in how data is handled. Price says that while there has never been a shortage of data, the ability to collect it has increased exponentially over the last few years, meaning information is being used to make better decisions that help impact the bottom line.
Advanced architecture
The IIoT is also designed to enable a far more flexible automation architecture, with secure wireless networks providing new sensing data streams.
This is according to Moazzam Shamsi, director of global solutions architecture, Emerson Automation Solutions, who says that architecturally, the IIoT provides a whole new set of possibilities; flexible architectures enable the secure integration of new and innovative sensors and scalable applications.
Shamsi also says pre-configured modular analytics means that data from new sensors can be interpreted closely, and coupled to where it is being measured.
“By eliminating data bottlenecks, information is delivered or available ‘on-demand’ within a secure enterprise framework. This enables collaboration, allowing subject matter experts to access the information which improves the decision-making process. We find that we can now collaborate with our customers, who allow us to view data, which allows us to advise them when they need to intervene and perform a maintenance or operational intervention, for example.”
This isn’t to say the Industrial Internet of Things is an entirely mature practice, however. And while the ‘hype phase’ might be over, a number of businesses are still struggling to understand the implications of the industrial internet.
According to Accenture’s Winning With the Industrial Internet of Things report, just 38% of business leaders say they completely understand the IIoT.
The Industry 4.0 Maturity Index
Paul Taylor, head of industrial products (UK) machinery safety at TÜV SÜD Product Service, adds that many companies still lack a coherent plan for implementing Industry 4.0 – a term coined by the German government, which refers to the fourth industrial revolution and incorporates the capabilities of the IIoT.
He says some companies only incorporate Industry 4.0 in selected areas of their organisations. However, in order to unlock all the opportunities offered by connected and smart production, efforts need to be extended to include logistics and customer service, Taylor says.
To address these challenges, German Academy of Science and Engineering, Deutsche Akademie der Technikwissenschaften (Acatech), developed the ‘Industry 4.0 Maturity Index’.
Taylor says the objective of the Index, which TÜV SÜD contributed to, was to provide companies with a tool that enabled Industry 4.0 to be introduced in “manageable steps”. The model, says Taylor, is designed to cover the entire value chain and focuses on the defined individual benefits for the company.
“What makes the Maturity Index so useful is that every single action delivers measurable benefits and the process is traceable at all times. On top of that, a team of external experts support companies by providing their individual know-how along every step of the process,” he says.
The Index is a systematic guideline, designed to support companies in the integration and continuous improvement of their IT and communication systems. It defines six successive stages: computerisation, connectivity, visibility, transparency, predictive capacity and adaptability.
Taylor explains that it also has a modular structure and covers five functional areas: development, production, logistics, services and marketing and sales.
Application of the Maturity Index covers three phases. “The starting point comprises analysis of the current maturity stage. Questionnaires, on-site factory inspections and workshops provide an overview of the current state of digitalisation.
“Phase two involves the definition of specific goals. This includes consideration of both the use of digital processes and corporate strategy. A gap analysis identifies the capabilities and resources still needed to achieve these goals.
“In the last phase, experts develop a digital roadmap to build up these capabilities. Actions are prioritised on the basis of a cost-benefit matrix.”
Next steps
So what happens when the majority of engineering firms have a roadmap for connectivity?
Honeywell’s O’Brien says the next step is to make the IIoT boring, scalable, practical, and just part of the normal course of how we approach software-based business outcomes. “It’s all about normalising it as a process,” he says.
Unfortunately, there are other obstacles that process firms need to overcome first: chief among these is a willingness to trust what the data is telling them.
“The process industry needs to take that significant leap into an environment where data can be used to make better decisions more easily. I think that’s the big risk some companies are still working through,” O’Brien says.
Fortunately, he believes that through a constant focus on execution, these issues can be overcome. “It is hard – there isn’t a silver bullet that will change everything overnight, but in five years we will be amazed with the progress that’s been made.”
Guiding hand
Bosch Rexroth offers a digital remedy for 4.0 phobia
Daunted by where to start your journey to a 4.0 world? Bosch Rexroth’s online Factory of the Future offers the chance to view online how the modern plant would function.
Hardware modules and functions are represented digitally to show how software solutions collect, transfer and process data to analyse, simulate and improve processes. Real-time gathering and processing of data from sensors in the factory enables production quality checks at the point of manufacture and continuous monitoring enables accurate machine and system health checks.
Practical illustrations include: cabinet free drives to reduce cabling; low energy, intelligent hydraulic power units; plus workstations with instructions adjusted to individual levels of training and knowledge.
The model demonstrates how smart factories make it possible to reconfigure production lines and facilities to fast-changing requirements. Instead of power cables, which effectively tie a machine to a specific location, machines are powered by inductive charging from the floor, with 5G connectivity for faster, more stable data transfer.
For those who prefer gradual change, there are reminders that digital technologies are highly scaleable and examples of how older machinery can realise benefits cost-effectively using a pre-configured plug and play IoT gateway.
Says a spokesperson: “What we’ve learned in developing the Factory of the Future is that when you consider what can’t be changed, surprisingly little remains: the floor, the walls and a roof. The rest of the factory: the machines, automation topologies, equipment, communication paths, even the people and how they work together, are subject to the changes demanded by modern manufacturing.”