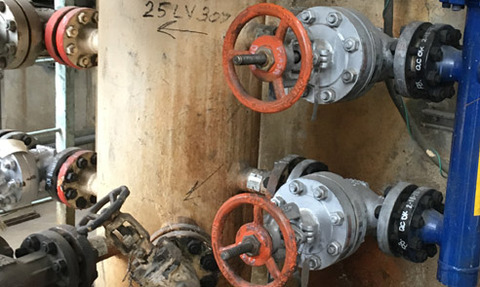
There isn’t a one-size-fits-all level measurement solution for tackling multi-interface levels of liquid, as Michelle Knott discovers.
Interface level measurement presents a big challenge throughout the oil, gas and petrochemical industries, where many processes result in two or more liquid phases ending up in a single vessel, where they have to be reliably separated.
There’s no one-size-fits-all solution for monitoring the boundaries in these multiphase systems. Instead, operators should consider a range of different level measurement techniques to find the optimum solution.
Making the right choice may not be straightforward, partly because these multiphase systems can be more complex than they first appear. For instance, there may be no true clean break at the boundary between two liquids. Instead, a layer of emulsion often sits between the two phases and the transition can be quite gradual.
Measurement specialist Magnetrol has just released a white paper that looks to unpick the problem and help users choose the right level measurement technology.
The key to optimisation for interface is solving the emulsion factor. No economical technology accomplishes all three level measurements
Magnetrol white paper
“Interface, like many other critical level measurements, will not be a one-size-fits-all solution,” says product manager Thomas Kemme.
Kemme also explains that good installation practice can play an important role in mitigating the emulsion problem as far as possible: “Emulsion layers are difficult to quantify. Often even if the customer knows there is one, they don’t know how thick it is. Based on our experience, we try to deal with the thickness of the emulsion layer by recommending the installation of the level device further from the entrance of a horizontal separator.”
The idea is to allow as much time as possible for the two phases to separate into stable, separate layers before trying to measure the boundary, but Kemme concedes that it may be easier to optimise the position of the sensor on a new application than it is in a retrofit situation.
“This may be more impactful for a separator being designed into a new application. Retrofits may not be capable of the ideal installation. With our level portfolio, we could help lead an end-user to the best technology if they have an understanding of the approximate thickness of their emulsion layer.”
Several level measurement techniques are typically in the running, depending on the application. As Magnetrol’s white paper explains: “The key to optimisation for interface is solving the emulsion factor. No economical technology accomplishes all three level measurements: the top of the hydrocarbon level (total level), while simultaneously measuring the top of the emulsion (water in oil) and bottom of the emulsion (oil in water).”
Guided wave radar (GWR) is a popular option, especially since it can track the top, total level of liquid as well as near to the top of the emulsion layer, says Magnetrol.
We try to lead with the application as well as customer requirements and then apply the correct technology based on our extensive level portfolio, as opposed to leading with technology
Thomas Kemme, product manager, Magnetrol
It can be a good option for applications that have a highdielectric fluid such as water on the bottom and a low-dielectric fluid, which includes most hydrocarbons, on top (the dielectric properties of fluids determine how much energy is reflected back to the sensor). The downside is that GWR can struggle if there is a very thick emulsion layer and too much energy is lost before the waves hit the bottom.
Magnetostrictive solutions use buoyant floats weighted for different levels. They can measure total level, as well as the bottom of the emulsion, says Magnetrol. Systems with the higher dielectric material on top are not a problem for magnetostrictive solutions. On the downside, they can be relatively complex to maintain, especially if the application means they are prone to developing a coating.
Like magnetostrictive systems, displacer-based systems also depend on buoyancy and this time they track the middle or average of the emulsion layer. They can only measure total level or the interface and involve moving parts that require maintenance. They can be also be inflexible in terms of range.
Capacitance is a technology that doesn’t have any moving parts and works by tracking the capacitance differences between low- and high-dielectric fluids. However, this technology requires careful calibration and the performance can vary with specific gravity, dielectric properties or viscosity. Probe coating can also be an issue.
Nuclear/radiometric technology deploys radiation to track different specific gravities and can be used in a vertical array to profile the changing composition of very thick emulsion layers. However, it’s relatively expensive and comes with additional regulation, maintenance and safety considerations.
Thermal dispersion measures the different thermal conductivity of the liquid layers. It’s economical and doesn’t need much maintenance, but it requires calibration and there’s generally less familiarity with the technology among users.
So there’s lots to consider and many users could benefit from leaning on the measurement expertise of their suppliers, as Kemme explains: “We try to lead with the application as well as customer requirements and then apply the correct technology based on our extensive level portfolio, as opposed to leading with technology.”
All at sea
A range of level measurement applications are being put into place as vessels opt for LNG as clean fuel in record numbers…
Shipments of liquefied natural gas (LNG) and liquefied petroleum gas (LPG) are increasing rapidly as countries around the world seek cleaner fuels. Bloomberg’s Global LNG Outlook says imports set new records in 2018 on the back of 8.5% growth, for instance.
In addition, recent commitments from the International Maritime Organisation to slash sulphur emissions from shipping by 2020 mean that vessels are opting for LNG as clean fuel in record numbers. Together these drivers mean that more LNG than ever is taking to the high seas.
This gives rise to a range of level measurement applications, depending on whether the liquefied gas is fuel or simply cargo. But in all such cases, level sensors need to overcome two challenges – the cryogenic temperature and low dielectric constant of LNG.
Clemens Hengstler, product manager with measurement specialist Vega, says that noncontact free space radar and probe-based guided wave radar (GWR) technologies deliver similar performance in terms of the sensitivity of the sensors with low-dielectric hydrocarbons, so the choice often comes down to ease of installation: “Free-space radar is simply installed from the top but the guided microwave [GWR] needs them to put a cable inside and, because the ship is moving, it has to be fixed to the bottom of the tank, making it problematic in maritime applications.”
He says Vega’s VEGAPULS 64 free space radar is ideal for LNG fuel tank applications, for instance. It can withstand temperatures as low as -196oC, thanks to its highlyresistant stainless-steel housing, which thermally decouples the instrument’s sensitive electronics from its surroundings.
In addition, its 80-GHz radar sensor can detect even tiny signals, which is crucial for materials with a low dielectric constant, since this is the property that determines how much energy is reflected back to the antenna for the reading.