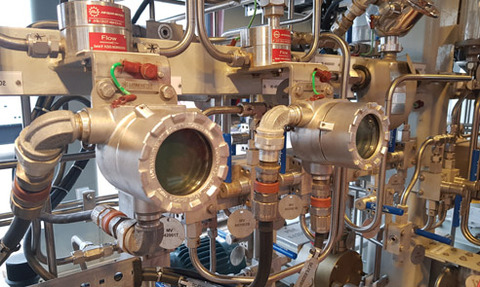
As sophisticated new measurement devices become available, businesses are unaware they could be sitting on a data goldmine, writes Tom Martland.
Interface level measurement presents a big challenge throughout the oil, gas and petrochemical industries, where many processes result in two or more liquid phases ending up in a single vessel, where they have to be reliably separated.
It’s easy to think, if something is working to the level that you expect, that it’s working as it should and, furthermore, to its greatest potential.
But, according to Neil Bowman, project engineer at flow measurement and fluid flow specialists TÜV SÜD NEL, “a common finding when visiting plants and production environments is that they are often not taking full advantage of the available technology”.
A common finding when visiting plants and production environments is that they are often not taking full advantage of the available technology
Neil Bowman, project engineer at TÜV SÜD NEL
Recently, huge leaps have been made in “wireless communication and powerful data processing”, says Bowman. “This can be an extremely powerful tool in the continual drive for improvement and process optimisation.” However, in many cases these devices are not being profited from.
“A recent trip to a spirits bottling plant highlighted just such a situation,” explains Bowman.
“The plant had purchased an advanced (and expensive) Coriolis flowmeter as a means to meter incoming product.”
However, he continues, inside the plant an entire team was noting down product density by hand on paper, with the aid of separate hydrometers, before entering this data, manually, once again, into a spreadsheet in order to calculate ABV (alcohol by volume).
“One of the advantages of Coriolis flowmeters is that they directly measure both mass flow rate and fluid density at the same time.”
Yet, he says, plant employees were unaware the meters had this capability. While its focus may not always be on optimisation, the food and beverage industry, like the petrochemical and pharmaceutical sectors, does place heavy emphasis on accuracy and, as Bowman [pictured] demonstrates, for very good reason.
In 2017, 1.2 billion bottles of Scotch whisky were exported from the UK, accounting for a gross return of c. £4.36 billion. Hence the weight placed by the beverage industry on precision.
“A measurement uncertainty of 0.5% on volume across the industry which would result in a financial exposure of around £21.8 million. This is obviously a highly simplistic example, but it illustrates the potential impact of mismeasurement.”
“Hydrocarbon-based products are high value and therefore there is a direct fiscal impact,” adds Bowman.
While in medical production, “precise timing and accuracy are critical to ensure repeatable, high-quality output. In this application, quality control is literally a matter of life or death.”
However, for industries less reliant on precision, investment in advanced technology is not necessarily wasteful. “Such systems can do far more than simply measuring flow rate, they can provide powerful diagnostic capability.”
Charles Wemyss, CEO at flow measurement engineering specialists Litre Meter, acknowledges that “having an efficient database relating to each process is a challenge most plants shy away from”. Yet it could reap huge rewards, he points out.
Bowman concurs with this view: “The application of machine learning techniques and even artificial intelligence has massive potential with application to process monitoring, quality and analysis of key performance characteristics such as calibration drift.”
Rise of the machines
Any AI relies on data: as much information as frequently as possible is the best way to improve its performance. Bowman’s team is already attempting to develop systems based on the progress made in this field.
“NEL is currently working with a number of companies developing products and systems that take advantage of this capability to implement distributed real-time measurement and analysis.”
Further applications of digital technology are being trialled by teams such as the Oxford Thermofluids Institute’s Osney Active Flow Control Group. The group has constructed a large test chamber which is capable of simulating 3D full-scale flow conditions.
Currently, the team is engaged in modelling a large civil aero engine under realistic operating conditions but the modular approach employed here enables line replaceable geometry changes. The group is actively controlling the leakage of air and thereby improving efficiency.
Bowman discloses that “in some industries, there is often a degree of inertia regarding the adoption of new processes or technology”. However, were it possible as in aerospace to identify consequent losses of productivity and demonstrate the potential to control efficiency drains in other industries, then there might be more enthusiasm, rather than the reluctance Bowman notes.
According to the Osney group, another of the aims of the facility is to enable rapid prototyping of various segment configurations “so that an understanding of the likely leakages/ heat transfers can be used to optimise the design”.
Of course, modularity is already on the minds of many manufacturers. Titan Enterprises, Litre Meter and Bu?rkert, as well as others, are highly aware of the positive influence of innovation in modular systems.
Litre Meter’s switch “reaped benefits to the customer including reduced prices and sharper lead-times”, Wemyss explains.
“In 2014 and 2015 we went down the route of standardising our design to allow for easy specification changes.” The change has meant that any customer has the option of “over 800,000 variants” at the outset.
Titan says that a new [modular] combination provides users with more versatility. The separation of the components of their newest flowmeter allows for the possibility of remote display reading – “particularly useful when the flowmeter is situated in an inaccessible or environmentally unfriendly location”.
Similarly, Bu?rkert believes that “a modular process control platform can be used to create a tailored solution for any manufacturing process”.
The watchword here is control. A system specifically built for a particular process allows for control over the greatest number of factors and, with internet aided remote connectivity, everything can be directed within one centre.
Trace elements
With smarter systems comes greater accuracy and little to no manual record keeping. However, Bowman emphasises still the importance of traceability.
TÜV SÜD NEL, he explains, hold the UK’s National Standards for Flow and Density. Any piece of measurement equipment can only have its uncertainty measured when compared with those standards.
“It must be possible to ‘trace’ a measurement device, normally through calibration, back to the national standard.”
Here again, businesses are incentivised to invest in higher quality technology, requiring very infrequent calibration and, through the connective solutions now on offer, without having to inspect the equipment manually and running the risk of increased downtime. Real-time measurement and analysis allow controllers to check on their systems at any point.
One of the aims of the facility is to enable rapid prototyping of various segment configurations so that an understanding of the likely leakages/ heat transfers can be used to optimise the design
The Osney Active Flow Contol Group
Identifying when in the process key performance characteristics such as calibration drift occur can aid in understanding of why they occur.
For example, contamination commonly derives from “entrained particulates in the flow such as dirt or sand, which in addition to deteriorating flow measurement performance can also wear or erode the flowmeter over time”, adds Bowman.
Without knowledge of the erosion of both accuracy and physical machinery, a meter would require frequent and often costly maintenance, culminating in replacement. However, equipment which can feed information in real time as to the point in the process at which a change arises saves money in both upkeep and manual inspection.
Further still, if a replacement was required, a modular system would result in the replacement of only one portion, rather than overhauling an entire production line. While expensive in itself, needless to say that the down time losses alone would be greatly damaging.
Data is key. While investment in new technology appears, in the short term, to be extravagant, the savings in efficiency, maintenance and manpower could be more than worth the outlay.
Keeping connected
Integration of key products is essential for effective flow systems, says Bu?rkert
Manufacturing processes requiring rapid temperature change can create efficiency problems, being energy intensive with a tendency to create bottlenecks.
Bu?rkert is seeking to address this with its new modular range of products integrating sensors, precision flow measurement devices and flow control valves.
For example, one of the major challenges in injection moulding is the production of parts that fall from the die ready for use and do not need additional processing.
An important contribution is made by vario-thermal control of the injection moulding tool. This allows production of plastic parts without distortion, with the right size and with high surface quality regarding gloss, haptic properties and lack of weld lines.
The main temperature regulation derives from the need to enable rapid changes between hot temperatures of around 180°C during the injection phase with cooler temperatures of approximately 100°C.
The key, says Burkert, is to position the valve switching station close to the tool, so the transition from hot to cooler temperatures involves only a very small exchange of water within the system.
In conjunction with accurate temperature measurement and flow control valves it is possible to create a very reliable and efficient process by implementing a modular process control platform. This enables the seamless integration of sensors, flow measurement devices and flow control valves within an existing installation.