How to ensure your operation is digitally mature for the 4.0 world
28 May 2019
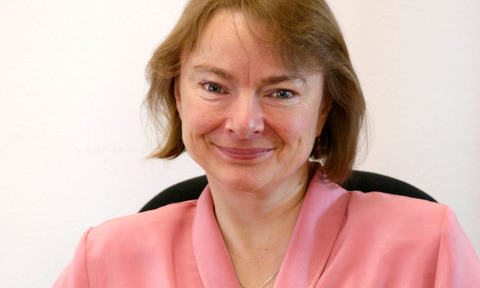
Clare Darlison of Idhammar Systems explains why manufacturers must take digital maturity seriously and how they can work towards achieving it...
Without commitment to change, you will achieve very little. According to Deloitte, leading organisations on the path to digital maturity are measured not only on their commitment to digital infrastructures but also on their readiness to adopt advanced technologies, including AI, VR and robotics, and see this seamlessly integrated in business operations.
There are clear cases of manufacturers doing this particularly well. For example, in 2019, Siemens opened its fully refurbished ‘Digital Experience Centre’ to illustrate practically how its industrial customers can successfully embark on a digital transformation journey.
In showcasing this to the world, Siemens is helping to lead the way whilst also demonstrating its own commitment to digital, providing an aspirational example.
Demonstrable benefits
Analysts McKinsey suggest manufacturing digitisation could boost heavy industry profits by three to five points, but only if organisations make new technologies work at scale. Frontrunner organisations who strongly believe in the value of digital when it comes to business processes are most likely to achieve this initially.
Additionally, as technology is set to underpin digital enterprise within the manufacturing industry, the ability to understand its importance will prove vital to a business strategy that not only enhances profitability but also ensures lasting results.
As 87% of UK manufacturers surveyed state that they are ready to invest in new technologies that will boost productivity, we expect to see the robotisation of important processes either within production or linked to it.
As technology is set to underpin digital enterprise within the manufacturing industry, the ability to understand its importance will prove vital
This can help streamline processes and ensure operations can continue on a 24/7 basis without the need for human interaction, helping to bridge the digital and physical loop within the process.
According to Tech Native, helping to further automate processes will ensure efficient production levels; it can also free up employee time to focus on new, less manual tasks that will deliver greater value to the business.
Better insights
Access to real time data can help provide actionable insights, helping organisations to make more informed, game-changing decisions. For example, understanding overall equipment effectiveness (OEE), which can impact your organisation’s bottom line and productivity levels.
Making the most of what digital can offer in terms of analytics provides better analysis of existing workflows and enable you to refresh your systems and processes whilst committing to scheduled maintenance.
Digital maturity is becoming essential for manufacturing organisations and ultimately, it’s very much a personal decision whether to fully embrace it.
Unfortunately, little more than one fifth of organisations surveyed by Deloitte rated themselves as ‘highly prepared’ to address the business models Industry 4.0 brings.
However, we predict that stragglers will soon look to introduce a more forward-thinking approach which in turn, will require an upskilled workforce and certainly one that is digitally confident.
This will of course involve the breaking down of barriers within the workforce, seeing cross-department collaboration and closer working relationships to fully achieve digital maturity that produces valuable results.
Clare Darlison is director of Idhammar Systems