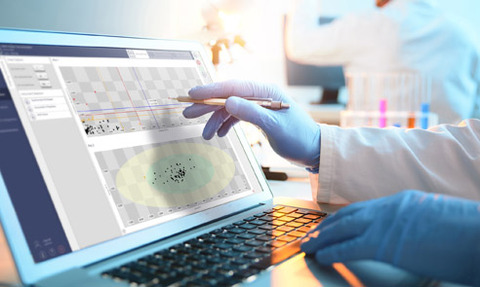
The influence of automation is being felt throughout the process industries. That includes safety aspects and working in hazardous areas, where the gains are clear explains Michelle Knott.
Industry is currently in the throes of the next wave of automation, with Industry 4.0 (I4.0) and the Industrial Internet of Things (IIoT) promising transformative change over the next few years.
A whole basket of technologies from machine learning and artificial intelligence to robotics and digital networking are bringing down costs, improving process control and asset management across the board. So what can this next generation of automation offer to process operators in hazardous area applications?
“To limit the exposure to a hazard, process automation can be used to control automated sequences inside hazardous areas. This may be inside a negative pressure glovebox enclosure or an entire room/area of the plant,” explains Jonathan Cannon, process engineering manager with project engineering firm Lorien Engineering Solutions.
“Process automation can be used to automate manual processes, alert the operators to any issues and safely shut down the plant/area to leave it in a state that is safe to access. In addition to automating the process, local condition monitoring can be used to continually monitor the hazardous area for dust, explosive gas or oxygen depletion.”
Process automation can be used to automate manual processes, alert the operators to any issues and safely shut down the plant/area to leave it in a state that is safe to access
Jonathan Cannon, process engineering manager, Lorien Engineering Solutions
While there’s plenty that automation can do to improve safety in hazardous areas, the constraints on equipment mean that there are also some specific challenges. “Implementing process automation in hazardous areas can be expensive if existing equipment is not suitable for the area of use. Existing equipment may need to be replaced or upgraded to meet area classification requirements,” says Cannon.
In the UK and Europe, that means complying with Directive 94/9/EC (also known as ‘ATEX 95’ or ‘the ATEX Equipment Directive’), which covers the requirements for equipment and protective systems intended for use in potentially explosive atmospheres. It sits side-by-side with Directive 99/92/EC (also known as ‘ATEX 137’ or the ‘ATEX Workplace Directive’) which covers the protection of workers potentially at risk from explosive atmospheres.
One way to control costs is to locate part of any automation system in a safe area, behind an intrinsically safe barrier. This means that only some of the equipment needs to be ATEX-certified. So, for example, monitoring instruments will typically need to be in the hazardous zone, while PLCs or human-machine interfaces (HMI) can be sited safely outside.
Batching usurped
While more conventional monitoring and control and can go a long way towards improving safety in hazardous areas, some of the emerging I4.0 techniques are potentially game changing.
For instance, Martin Gadsby, director at Optimal Industrial Technologies, notes that monitoring chemical processes based on Process Analytical Technology (PAT) enables the sort of real-time, in-line and on-line quality assurance that can enable operators to swap batch processes for continuous manufacturing, since they no longer need to wait for lab results or spot checks to ensure quality control. This in turn may even make it possible to switch chemistries and adopt an optimised synthesis pathway that might previously have been ruled out as too hazardous in a batch situation.
For example, a strongly exothermic process may be too dangerous to run in a batch, because a runaway reaction could be catastrophic with the quantity of hazardous material involved. However, it may be possible to produce the same quantity of product per unit time using a continuous, ‘flow chemistry’ approach, where only a few grams of product are in a hazardous state at any one time.
“This is possible simply because with a flow chemistry process there may be only a few grams of material in the hazardous state at any one time, rather than, say, a tonne,” says Gadsby. “The process of course has to be treated as hazardous, with all the necessary automation and operational infrastructure and oversite. However, the overall risk has been mitigated by many orders of magnitude.”
“For all [such] situations the hazard has to be assessed and the correct intrinsically safe or explosion proof automation hardware and instrumentation installed. However, a PAT system such as synTQ from Optimal can provide yet further protection in that it can detect process deviations (including a process moving towards a more hazardous state) using multivariate techniques, this often not being possible with traditional univariate automation systems. By having this early detection system, the risks can be further mitigated.”
Bring on the robots
Robots are another area of interest for those working in hazardous areas. “Robots are increasing being used in hazardous areas where there are toxic, high-temperature, combustible or flammable atmospheres present. These areas pose significant health and safety issues for operators working in these areas,” says Cannon.
“Robots are ideal for use in these hazardous environments as people are removed from direct exposure to the hazardous environment. However, robots used in combustible or flammable atmospheres must be certified against the ATEX equipment directive to ensure that they are not a source of ignition.”
Traditionally, personnel entering confined spaces to perform cleaning prior to inspections has been the only way to implement a detailed legislative inspection, de-sludge or clean for product change. There are inherent risks
Fintan Duff, managing director, Re-Gen Robotics
Emergency services and the military have led the way in the use of robots in dangerous situations, but the offshore industry is another area showing a keen interest in robots. In May 2017, a partnership between Austrian robotics firm taurob and a research group at the Technical University Darmstadt in Germany won the ARGOS challenge set by Total to design the first Autonomous Robot for Gas and Oil Sites. The aim of ARGOS is to obtain a robotics solution on an industrial scale by 2022.
There are also plenty of less high-profile areas where a robot could be the safest solution. Tank cleaning is a good example. Manual tank cleaning contributes to around 25 avoidable deaths within confined spaces in the UK and Ireland each year.
Re-Gen Robotics, sister company of the Re-Gen Waste Ltd materials recovery facilities, wants to eliminate the risk with the recent launch of what it believes to be the first and only remotely controlled, ‘No Man Entry’ robotic tank cleaning company in the British Isles.
The company has invested £1.5 million in two purpose-built, fully compliant, Ex Zone 0 rated machines; one designed to de-sludge, wash and clean large-scale tanks and a second, lightweight and compact unit suitable for use on smaller sites and underground storage tanks and containers, including petrol forecourts, interceptors and process tanks.
Re-Gen Robotics’ unique, closed-loop cleaning system is fully compliant with existing safety legislation and can reduce cleaning time by up to 45%, significantly decreasing downtime and loss of production whilst the facilities are not operational. The Ex-zone rated equipment provides predictable cleaning times, meaning the tank is brought back into operation quicker and reduces the need for additional tank capacity, permits and extra support teams.
MD Fintan Duffy says: “Traditionally, personnel entering confined spaces to perform cleaning prior to inspections has been the only way to implement a detailed legislative inspection, de-sludge or clean for product change. There are inherent risks to entering a hazardous confined space and although safety regulations and standards are high, occasionally accidents occur, due to human error or failure of safety devices.
“At no time during the Re-Gen Robotics cleaning process will there be a need for human presence in the confined storage container. Our technical operator remains a safe distance away in the Zone 2 control unit, where they can monitor activity and progress through a series of ATEX cameras fixed to the equipment placed inside the tank being cleaned.”
Once cleaning is complete, the robot washes itself down and exits the container via its ramp before returning to the control unit.
“At Re-Gen Robotics what we have created is truly gamechanging conditions for the tank terminal sector,” says Duffy