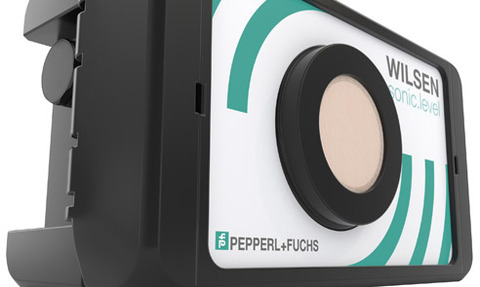
Automation and digitalisation are dominating the environment but the pressure to marry efficiency with budgetary limitations is ever-present.
Schneider Electric’s Rethink Energy report detailed the scale of emissions attributable to wasted energy, asserting a 30% reduction in such waste can convert into a 10% saving in operating costs for a business.
In addition to commercial incentives, the Environment Agency’s monitoring certification scheme MCERTS ensures industry complies with emissions monitoring quality requirements. Central to this is effective level measurement.
Dale Snow, process instrumentation & AP business manager for Siemens, emphasises the crucial contribution of accurate testing to industry and environment.
“The two biggest impacts level measurement can have on the environment are safety and environmental monitoring. Level measurement is often used to monitor discharge flows, helping the end user comply with their PPC discharge permit under the EA’s MCERTS scheme.”
The biggest challenge will be maintaining a competitive edge with increasing price pressures while also developing technologies which deliver improved features, data and performance
Dale Snow, process instrumentation and AP business manager, Siemens
Fortunately, powered by demand and some exponential advances in recent years, level measurement has been advancing significantly. Two significant factors – one dating back several decades, the other of much more recent vintage – have been radar technology and the onset of digitalisation.
Siemens and VEGA have long been at the forefront of radar development in level measurement; one boasts experience based on the operation of one million instruments worldwide, the other claims more then 0.55 million sensors working in diverse level applications worldwide.
Nearly 30 years ago VEGA unveiled the first production-ready radar level gauge, followed six years later in 1997 by the first two wire radar instruments and then seven years later, the enhanced sensitivity Vegapuls 68 sensor, capable of tackling bulk solids.
For Siemens’ Snow, the latest developments are among the most interesting because of their potential to deliver.
“From my view point the most interesting level trends are mainly in high frequency > 60 GHz radar. This has opened up some new applications and also challenged the technologies used today, but it remains to be seen if it will be as reliable and robust and how much maintenance it will require over the period of its life in comparison to some of today’s technologies.”
Indeed, VEGA’s Vegapuls 64, billed as the world’s first 80 GHz radar, is being hailed by its creator as ‘a radically new era in radar measurement technology’. VEGA MD Ray Tregale [pictured] has no doubt that non-contact radar technology will be the game changer in many mainstream industries.
Whereas it was once seen as a specialist and complex technique, it is he says becoming more commodity-based.
“It used to be the preserve of difficult and challenging (or ‘high demand’) applications and processes, it has now become much closer to the industry standard choice for level measurement, because it is so versatile and simple to use – now simpler than ultrasonic devices with new 80Ghz focused sensors,” says Tregale.
He foresees radar replacing many traditional level technologies because of its superior performance and low prices – from under £400 for a new compact 80GHz device, he explains.
“The new radar chip we have just developed really does look set to make the real difference, by reducing cost and complexity for ‘standard/ simpler’ (or ‘low demand’) applications.”
Snow concurs that process industry instrumentation is moving closer to becoming a commodity although individual expertise still counts when specifying factors such as exotic materials, pressure, ex approvals and Safety Integration Level (SIL IEC 61511/61508).
Competition savvy
“The biggest challenge,” he predicts, “will be maintaining a competitive edge with increasing price pressures while also developing technologies which deliver improved features, data and performance.”
Despite the advances, investment in more complex products is a concern to firms who may feel they lack the financial means and personnel necessary. Digitalisation however brings a whole raft of benefits to increased automation, outlines Tregale: “Giving customers more information about their processes, e.g. through sensor status and measurement reliability. Proactive maintenance planned outages rather than reactive ones, improved productivity, better use of resources, less wastage – if a process unexpectedly malfunctions without warning, associated costs (waste, time, personnel, clean up) soon mount up.”
Data yielding potential, says Snow, is often a significant generator for level measurement industry interest in innovation. This also requires raising awareness among customers.
“Most instrumentation today is still just providing a main variable via switch contact or mA signal. The digitalisation trend is moving customers towards “more data’’ which has often always been there, just not used,” he states.
“Using the available data is interesting to end users for many reasons e.g. improved processes, predictive alarms, etc. There are immense possibilities with digitalisation such as predictive maintenance and improved efficiency.”
Sustainability means longer service, seeing instruments as an investment, ensuring they deliver a long life span but also remain adaptable to new requirements. That means legacy support for devices
Ray Tregale, managing director, VEGA
This can be achieved, says Snow, if the infrastructure is fully digitally integrated and IIoT (he cites Siemens’ MindSphere cloud-based technology) employed for data storage and analysis.
The benefits accruing are clearcut. Firstly accuracy – unlike analogue instruments there is not the likelihood of transmission and input ranges of two communicating instruments being out of kilter. Secondly, digital instruments can combine different measurements. For example, Micronics’ new UF AV5500 area-velocity flowmeter employs a submerged ultrasonic sensor that continuously measures both velocity and level in a water channel. Other instruments combine pressure or temperature and other values.
There’s also the opportunity to reduce the human element, providing a safety enhancement – reducing employee exposure to the ‘dirty, dangerous, distant and dull’ – as well as an efficiency gain by removing degrees of manual, human intervention.
Pepperl+Fuchs’ Wilsen.sonic.level sensor system integrates ultrasonic measurement for fill levels, recording data at regular intervals and uploading this with geolocation to the internet. A battery-operated wireless sensor allows the instrument to be used in mobile containers to ensure fill levels for containers, tanks and silos can be managed remotely. Also, in the crude oil tank measurement market, advances offered the likes of Emerson’s Rosemount range have significantly reduced the incidence of injury and fatalities.
Sustainable sense
As ever, transitioning to a fully digital level measurement operation is a daunting prospect for smaller firms especially. Some practitioners recommend the use of HART (Highway Addressable Remote Transducer) technology to superimpose digital signal on a standard 4-20mA analogue device.
Tregale offers a qualification regarding the benefits: “With a lot of sensors already providing HART information, although it’s quite a slow speed protocol by modern standards. It is possible to use this information to enjoy an easier transition. However, newer protocols and platforms can be easier to integrate [although its] asset management functions are also useful for digitising maintenance and servicing,” he assesses.
For a more comprehensive approach, he suggests, look first at updating parts of a plant which would benefit quickly and those that are more critical. Also, web-based solutions that can provide information without the need for expensive or large scale back-end modifications with options including integrated LAN or WAN in controllers, web hosted data and supply planning.
However, transition remains as much a question of sustaining as spending, cautions the VEGA MD.
“Sustainability means longer service, seeing instruments as an investment, ensuring they deliver a long life span but also remain adaptable to new requirements. That means legacy support for devices, not just throw it away to upgrade.
“For example when we offered Bluetooth communication for set up and maintenance, we provided it not just from new sensors, but also able to retro fit to all our transmitters (without firmware change) manufactured from 2002 – that’s up to 17-year-old legacy devices with Bluetooth communications, without firmware or software changes.”