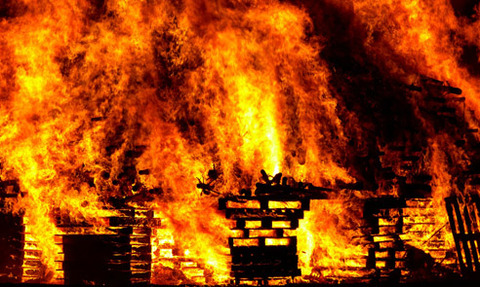
Health and safety at work is in the spotlight once again. So how do process managers ensure that their compliance is all it should be, asks Greg Pitcher.
Whatever the ultimate outcome of the Bosley Mill prosecution case, it highlights, says Keith Plumb, associate consultant at process engineering design consultancy BPE, the need to prove one has taken reasonable steps to prevent explosions in factories.
For example, corporate manslaughter charges can lead to fines of up to £20 million while gross negligence manslaughter can be punished with lifetime jail terms. Says Plumb: “It could wipe your business out completely.”
Focusing the minds of process industry bosses on these very real risks to their own freedom and livelihoods is an important part of preventing more tragedies, he adds.
“People never think they will kill people but the message might get through if you show them they could end up in court and lose their business.”
With all the powerful equipment and dangerous substances to be found in process engineering plants, preventing fires and explosions may appear difficult, but a critical factor in many major incidents is something that can be routinely found in all walks of life – dust.
An old concept that is still prevalent, especially in North America, is focusing on electricity. But research showed just 3% were ignited by electrical sparks
Keith Plumb, associate consultant, BPE
When hot, dust can act as kindling. And when airborne, it can turn a small fire into a catastrophic explosion. Yet despite the risk, dust is often found in large quantities throughout process plants.
A report by the US Chemical Safety and Hazard Investigation Board found that a 2008 incident at an Imperial Sugar refinery in Georgia killed 14 people and injured 38 more when an “explosion was fuelled by massive accumulations of combustible sugar dust throughout the packaging building”.
So what is best practice in controlling the risk of dust explosion in factories? “The Dangerous Substances and Explosive Atmospheres Regulations say the number one priority is to remove the explosive substance, and the second is to replace it with something less dangerous,” says Plumb. “Both of these steps are a bit tricky if you are creating dust as part of a process. So if you can’t do either of these, the next priority is to minimise the amount of dust you have, and this comes down to housekeeping.”
Under the regulations, process firms should carry out risk assessments to classify different parts of their buildings according to their likelihood of dust being present in a dangerous concentration. Then they should specify machinery suitable for each zone.
“If you have a dust cloud then you can’t have a source of ignition,” says Plumb. But he adds that people don’t always think about ignition in its broadest sense.
“An old concept that is still prevalent, especially in North America, is focusing on electricity. But research carried out in Germany looking at dust explosions showed just 3% were ignited by electrical sparks.”
Plumb suggests contracting a company that owns the British Standards for all key potential sources of ignition – including friction heat, mechanical spark and static electricity.
Once identified and understood, there are a number of steps possible to eradicate or mitigate these risks. Clearly preventing explosions is a complex process.
“It is not straightforward,” says Plumb. “That’s why companies without much money find difficulties.”
But he goes back to the point that the most effective intervention is also the cheapest – keeping a factory clean.
“That is not being done so there is an awareness issue,” he says. “A simple message has to be got across.”
Plumb hopes high profile court cases such as that following the Bosley disaster will help to focus minds in the sector. But he also calls for more reporting of minor incidents and near misses.
Mike Bradley, director of The Wolfson Centre for Bulk Solids Handling Technology at the University of Greenwich, has investigated a number of cases where fires have started in equipment rated under the EU ATEX Equipment Directive as suitable for use in potentially explosive atmospheres.
“There have been quite a few incidents where fires have started in ATEX-rated equipment,” he says. “This is equipment rated to say it won’t cause an ignition source, yet on a number of occasions it has.”
Bradley has discovered a pattern of insufficient analysis of equipment’s capacity to create a source of ignition.
“In one example, on a biomass handling system, there was a screw feeder at the bottom of a silo,” he says. “A means of keeping the shaft in place failed and the shaft contacted the end casing and rubbed slowly against it.
“In the standard for assessing ignition hazards, it says rubbing at less than 1m per second will not create a spark strong enough to ignite a dust cloud. This was rubbing at under 0.2 m per second.”
Indeed it did not directly generate a spark. But the outside of the conveyer was covered in explosion control’s old foe – dust – and the heat generated by the slow mechanical friction could not get away.
There have been quite a few incidents where fires have started in ATEX-rated equipment [which is] rated to say it won’t cause an ignition source, yet on a number of occasions it has
Mike Bradley, director, Wolfson Centre for Bulk Solids Handling Technology
“The heat built up, and the dust smouldered and dropped on to a dusty floor, causing a secondary explosion.”
Nobody was hurt on this occasion, but Bradley says it was not an isolated case.
“On a few occasions, it seems fires have been started by slow moving equipment where something mechanical has failed and rubbing has caused a fire or an explosion.
“The standard does cover this but it has not been picked up by people doing ignition hazard assessments.”
He calls for process plant specifiers to carry out their own due diligence on the ignition hazard assessments carried out by notified bodies handing out ATEX certificates.
“In theory they shouldn’t need to do this but in practice there have been lots of incidents,” he says. “It pays to look for potential for mechanical failure that has not been picked up.”
Bradley agrees with Plumb that raising awareness is critical and is working with the Solids Handling and Processing Association to run a one-day course on fire and ignition risk, looking beyond the ATEX law.
Tony Reynolds, compliance manager at Lorien Engineering Solutions, says lessons can be learned from abroad as well as closer to home.
He says an investigation is underway into an explosion at a plant in China that killed 78 people on 21 March 2019.
On the other side of the world, the US Chemical Safety and Hazard Investigation Board recently released a new digest about the importance of operator participation in preventing accidents.
“It stipulated that missed opportunities for operators to participate in process safety activities contributed to incidents,” says Reynolds.
“Managers should take steps such as empowering operators to provide input on how the work is performed; enabling safety issues to be raised without fear of reprisal; and providing more training opportunities.”
He hopes the industry will learn from its disasters. “Accidents are still happening, and these may have been a trigger within organisations to revalidate existing risk analysis studies or start up procedures.”