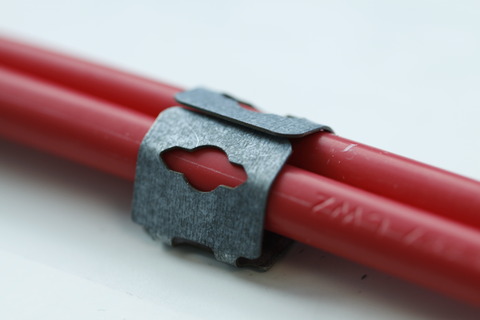
The focus for electrical safety and testing issues is shifting attention from causes outside the factory or plant to focus within it and on the smarter devices upon which it relies. Yet the same principles for good practice apply.
“In an increasingly electrified world, the role of electrical and design engineers is to keep everything running smoothly – power quality is integral to that and understanding the root cause of today’s electrical issues is imperative to achieving good power quality.”
So says REO UK managing director Steve Hughes. It is a salutary reminder that, while we are now moving deeply into the 4.0 era, much is dependent upon maintaining and building on traditional electrical knowledge.
As an expert in this field, Hughes emphasises its importance to the modern industrial world in his latest publication The Past, the Present and Future of Power, stating that one thing unifies all modern technology: the need for power.
The equipment power supply contains a rectifier that converts the AC from the mains network to DC. This is necessary for these lower voltage applications but the conversion process can create problems that intensify and escalate over time
Steve Hughes, managing director, REO UK
Nearly two thirds of power quality issues across the globe, he cites, are the consequence of harmonic distortions from non-linear loads that create problems within cabling systems or motors and transformers.
Previously factories’ focus has been on the maintenance of power supply to equipment in the event of blackouts caused by faults in the power grid – a challenge overcome with backup generators and uninterruptible power supply systems, he points out.
Fast forward and today, the power problems are located within the modern plant. Hughes explains that heavier machinery often depends upon alternating current direct from the grid. Synchronous motors, for example, will regulate their rotor speed to AC supply frequency.
Electronic devices as well as low voltage applications are incompatible with AC, though, because they are made to rely on average power value. Also, as AC has a natural fluctuation, this is insufficientlyconsistent for those devices that run logic operations, for which direct current is used.
“Here the equipment power supply contains a rectifier that converts the AC from the mains network to DC. This is necessary for these lower voltage applications but the conversion process can create problems that intensify and escalate over time,” he explains.
Systems such as switched-mode power supply and variable speed drives have ensured considerable progress in the manipulation of electric currents. But they do bring the threat of radio-frequency interference and harmonic currents, stresses Hughes.
There’s clearly an efficiency aspect to this with the obvious impact on the all-important issue of downtime and its avoidance. There’s a safety aspect too, warns Michael Kenyon, technical manager at testing and certification experts Bureau Veritas.
Increasingly, the direct current from the proliferation of electronic devices and renewable energy sources adversely affects residual current devices (RCDs) reliant on alternating current.
Given that RCDs’ purpose is to act as a circuit breaker to prevent life-threatening harm from electric shock, this represents an appreciable risk that may be unintentionally exacerbated by the rise of interest in renewables, says Kenyon.
“Modern electrical installations are now more than ever incorporating technologies and products that manipulate the current wave forms. These devices such as Solar PV and electric vehicle chargers could be leaking (Direct Current) back into the electrical system and saturating the iron core of the AC type RCDs which are not designed to handle it,” he explains.
“This is a particular problem when dealing with poor quality electronic equipment or substandard installations as DC leakage current can be created by faulty equipment such as Solar PV, EV chargers, variable speed drives, and even faulty mobile phone chargers or USB sockets. Inevitably, we’re seeing RCDs being increasingly affected by DC – putting many people at risk.”
The Institution of Engineering and Technology’s (IET) 18th edition of its wiring regulations sought to address the problem but Kenyon questions whether directives go far enough, for example in the recent rewrite of 531.3 of BS7671.
“The rewrite of 531.3 has certainly led to an increased awareness of the different type of RCDs but in terms of promoting best practice it just doesn’t go far enough in recommending the use of A type RCDs.”
Devices such as Solar PV and electric vehicle chargers could be leaking (Direct Current) back into the electrical system and saturating the iron core of the AC type RCDs which are not designed to handle it
Michael Kenyon, technical manager, Bureau Veritas
In fact, Kenyon says, regulation 531.3.3 states that for general purposes, Type AC RCDs should be used coupled while there is the disincentive for Type A RCDs in that these are less readily available.
They are also more expensive, so not surprisingly 90% of devices online are still AC type, admits Kenyon.
“Specifying the correct RCDs can be a technical and complicated area, and currently there’s a knowledge gap within the electrical industry about the risks of using AC type RCDs in modern installations. That’s why it’s important, now more than ever, to ensure every electrical installation is safe and fit for use – and the best way to do this is through regular testing and inspection.”
The new wiring regulations are spurring manufacturers to offer new product ranges to ensure assurances on compliance.
Cable management experts HellermanTyton responded to the IET wiring regulation 18th edition’s insistence that plastic clips should not provide the sole or even main support for cables with a new range of metal fisings.
Its Fireproof Plate series are made of galvanised steel material and tested in up to 830°C for as long as two hours. Both these and the Spring Steel Clip Series have both been tested at Exova Warrington Fire Test lab to ensure they are compliant with specification BS 50200: 2015.
While the fines around electrical safety have increased markedly recently, process safety managers and employees will do well to return to the seven key principles outlined in these pages previously by Martindale Electric marketing director Andrew Holland.
These are: isolation of power sources during maintenance; compliance with HSE document GS38 which combines all relevant test equipment standards; extra care testing multi-meters; use of proving units to test voltage indicators before and after work; robust safety procedures; proper training in procedures; and don’t assume employees have the appropriate equipment – test for failures.
While the legislative parameters for electrical safety and the sources of greatest danger are constantly changing, these offer a template for good practice regardless of changing circumstances.
Grey elephant
Waste electrical and electronic equipment is an issue that can no longer be ignored. But more clarity is needed.
Global consultants RINA’s Electrical and Electronic Equipment and the Environment conference has highlighted the problem of waste electrical and electronic equipment (WEEE) as “the elephant in the room” for industry.
Kevin Bradley, secretary general of BSEF, The International Bromine Council, is forthright in his criticism.
“No one is collecting enough and an awful lot of equipment is still stuck in people’s drawers – they don’t know what to do with it. In terms of recyclers, there isn’t [one] single company that processes plastic waste – especially that containing brominated fire retardants (BFRs),” he says.
“There are a lot of grey areas, and material is exported, with companies washing their hands of the responsibilities.”
Plastic shred that potentially contains fire retardants could be sent to a specialist processor outside the UK but at present for the EU it can take six months to get an export licence. Shipping it outside Europe for process and return has resulted in flame retardants being found in food packaging.
Government is examining the potential for a new system of Extended Producer Responsibility (EPR) for packaging but Ben Storer, senior technical advisor at recycler Valpak, offers a warning:
“The biggest change will be the move to full net costs,” he says. “This means producers will be expected to pay the entire costs for collecting, recycling and disposing of packaging in future, rather than just a contribution towards it.”