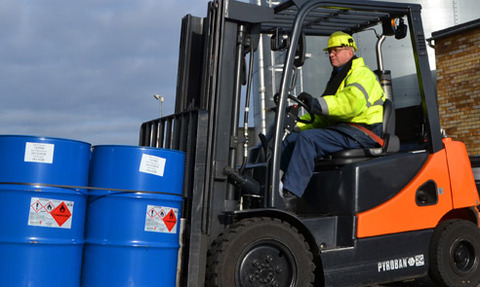
Downtime has taken on a new meaning and that raises new issues for ATEX compliance.Two experts explain the implications in their specialist areas, while a third adds a caution about the dangers of static electricity.
There’s never a time when safety can be taken for granted when working in hazardous process environments. Yet the lengthy lockdowns enforced by the global pandemic have created a new dimension.
As Darren Boiling, materials handling manager for the safety company Pyroban [pictured below] explains, lockdown has meant more firms are simultaneously contending with the challenge of reinstating operations and the dangers involved.
“For some operations handling flammable materials with lift trucks, restarting operations presents additional risk. Meanwhile others under financial pressure must now take special care when rolling on contracts or purchasing used ATEX lift trucks,” he states.
In the chemical and petrochemical industries, a large proportion of incidents occur during start-ups or shutdowns while manufacturing operations restarting after idle periods are more susceptible to fire, explosion, or machinery breakdown, cautions Boiling.
“Even a simple warehouse storing chemicals or paint in sealed containers should have a pre-start plan and safety check too. There may still be additional detail to consider when it comes to restarting operations following lockdown which use ATEX compliant mobile equipment in potentially explosive atmospheres.”
The Government may have temporarily relaxed rules regarding annual MOT checks for vehicles in general but it’s a different story where those used in an ATEX-related context are concerned.
Boiling points out that guidance from the British Industrial Truck Association, Fork Lift Truck Association and the Health and Safety Executive was adamant that it remained essential to check whether ATEX trucks required their examination and/or annual safety audit (Ex-ASA).
As the guidance states clearly: “Scheduled maintenance, repairs and statutory inspections must be considered essential ongoing activities.”
Thus, he says, Ex-ASAs are still considered essential for trucks working in Zone 1, 2, 21 or 22, before the equipment is put back into use. Pyroban’s Ex-ASA also supports compliance with the ATEX 2014/34/EU Directive through the EN 60079-17 standard.
Cranes, access platforms and scrubber driers used in Zone 2 areas to temporarily to get the operation back up and running should also have the correct levels of protection.
The most effective way of ensuring equipment cannot accumulate static electricity is a dedicated static grounding that monitors ground connection to components at risk
James Grimshaw, marketing manager, Newson Gale
Contracting business opportunities and rising costs associated with post-lockdown operations has encouraged interest in short-term hire of expensive but essential equipment.
“Short-term hire equipment used in areas where explosive atmospheres may occur, but not in such quantities that would require full ATEX compliant Zone 2 (or Zone 1) solutions, should have some form of protection. Gascheka Zone 3 is a gas detection system that can be fitted quickly and easily removed again in these cases,” explains Boiling.
Likewise, there is a demand for used materials handling equipment. Pre-owned explosion proof lift trucks can be useful and affordable additions to potentially explosive operations, he acknowledges, but these must be matched with explosion risk, usage and be certified as in safe working order.
“For instance, has the truck been regularly maintained by [an] engineer who used the correct parts and service regime? Was the truck’s safety system audited on an annual basis by a safety inspector?”
Understandably, some firms are opting to roll on existing ATEX contracts.
“It is still vital to check when a safety audit was last conducted and conduct an Ex-ASA if it’s due. Failure to do so could have big implications for both safety and compliance.”
Finally, there’s the human aspect. Are the operators conducting proper inspections to ensure equipment is fit for duty and do they need training on new ways of cleaning and sanitising equipment?
James Grimshaw, marketing manager at Newson Gale, cites one case where a process operator working on a pneumatic conveying system heard a crackling noise when powdered material was being transported between a classifier and loading hopper. During investigation, they received a significant static shock after contact with a section of the duct.
Explains Grimshaw: “The most common method of electrostatic charging on such process operations is due to tribo-electrification, which is simply the contact and separation of the powder with the walls of the processing equipment, the powder molecules itself or other factors that can cause charging, like surface contaminants.”
Inspection revealed the section was not suitably grounded. When tested it was found that it had a resistance path back to ground well in excess of 1011 Ω, exceeding recommended resistance of less than 10 Ω for metal plant items in good contact with ground.
There may still be additional detail to consider when it comes to restarting operations following lockdown which use ATEX compliant mobile equipment in potentially explosive atmospheres
Darren Boiling, materials handling manager, Pyroba
This resulted from a single grounding clip that had not been properly installed. Piping between the two ducts acted as an isolated conductor resulting in the generation and subsequent accumulation of charge. Lack of continuity to ground meant that the charge could not be dissipated, allowing an excessively high voltage potential to develop on the duct which eventually discharged onto the operator.
Adds Grimshaw: “The most effective way of ensuring equipment cannot accumulate static electricity is a dedicated static grounding that monitors ground connection to components at risk.”
As training is a key component, so is Personal Protective Equipment. Given the extra potential dangers of restarting from lockdown, says Mark Lant, technical expert at ProGarm, it is essential that workplaces are aware of key regulations.
Its recent study revealed nearly eight out of ten industry workers surveyed were unfamiliar with relevant legislation for protection against Arc Flash – a commonly-occurring type of electrical explosion within process sectors capable of generating thermal energy at temperatures of up to 19,000°C.
Several regulations merit mention in hazardous process operations. One, IEC 61482-2, is “the overall standard covering clothing that protects against the thermal arc hazards of an electric arc and covers many aspects of garment design and testing”.
“PPE must pass one of two tests: Open Arc or Box Arc to measure the ATPV or the new ELIM ratings of a garment. ATPV values are calculated from a prediction of the incident energy level of an Arc Flash, at which there’s a 50% probability that the heat transfer will cause the PPE material to break open... new ELIM ratings are measured to ensure a 0% probability,” says Lant, adding a product’s ELIM rating could be different from its ATPV rating.
It’s crucial to realise, he adds, that a product’s ELIM rating could be different from its ATPV rating. Other regulations to note are:
- BS EN 1149-5, the European Standard for garments that protect against electrostatic discharge in areas with a risk of explosion; materials must not enable electrical discharges that ignite explosive atmospheres, outer fabric must be made from antistatic materials covering all non-complying materials while non-dissipative materials must not exceed 50mm
- BS EN ISO 14116 covers outerwear worn over other protective garments to limit flame spread and duration
- BS EN ISO 11612 for clothing, offering limited flame spread and protection against radiant heat, convective heat and splatters of molten metal. Material must not ignite, melt or shrink more than 5% with heat resistance at 180°C. Numbers after prefixes A, B, C, D, E and F indicate fabric performance
- BS EN 13034: Coating protection against liquid chemicals must repel contaminants and preserve clothing properties Far from becoming a casualty of post-Covid cost cutting, ATEX expertise is likely to be in greater demand in the era ahead.