Listen for emission and you reap the benefits
10 Mar 2021
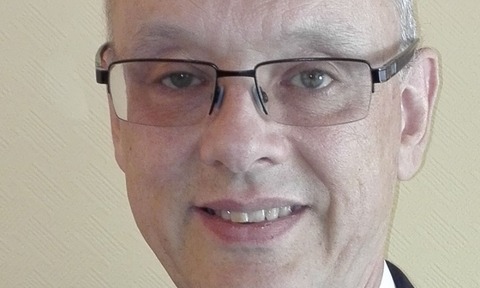
Acoustic emission testing detects incipient defects in pressure equipment and reduces the risk of failure and preserves the integrity of plant components., explains Klaus Michael Fischer at TÜV SÜD...
The German Regulation on Health and Safety in the Use of Work Equipment (BetrSichV) requires periodic inspection and testing of pressure vessels, tubing, and other pressurised components.
The focus is on aspects such as strength or leakage as applicable as well as interior inspection, i.e. examination of the inside of pressure equipment for damage mechanisms including cracking and/or corrosive attacks.
The more detailed the information that can be gathered about the relevant component, the better maintenance measures can be planned and shutdowns of plants and production losses effectively avoided. These advantages benefit plant managers who rely on a fast and reliable digital test method, i.e. acoustic emission testing (AT).
A refinery manager decided to rely on AT instead of visual inside examination for the periodic technical inspection (PTI) of the large vessel of a C4 column. Under this method, there was no need to take the system out of operation or clean the column for inspection. Neither did the method require other costly or time-consuming measures to ensure occupational health and safety and environmental protection, or cause costs due to production losses from a system shutdown.
The refinery manager commissioned the scaffolding of the column. At the intended positions of the piezoelectric sensors for AT, the vessel insulation was removed over an area of 20 cm2. Overall, a total of 88 AT sensors were used on the column. Sensors were distributed across the entire outside surface of the vessel, and then attached with the help of magnetic holders and couplant. Although the number of sensors was small in relation to the size of the vessel, it sufficed to create a digital twin of the entire structure.
Producing test pressure and recording sound waves
The refinery manager pressurised the column to a specific test pressure. To replace visual examination of the inside of the vessel, the test pressure must be at least 1.1 times the maximum service pressure over the last twelve months. Pressurising the column, including online monitoring, took around twelve hours.
Waves are caused by active discontinuity, i.e. defects such as cracks in the material, which grow minimally under the applied pressure, causing short-term displacements. These sudden motions set the surrounding material structure in vibration, causing a transient, elastic acoustic wave. This wave propagates from its point of origin to the sensor’s piezoelectric crystal, which transforms it into electric signals. These signals are recorded by a test computer, presented graphically in the digital twin and finally interpreted by experienced test engineers.
This method enables discontinuities to be detected in the material structure before they can cause critical states. In many cases, AT enables far more accurate statements to be made than conventional visual examinations or pressure tests.
This also applies to the evaluation of non-critical inhomogeneities or micro-cracking that do not propagate in operation and thus can be left unchanged. Based on the recorded data measured on the C4 column, TÜV SÜD recommended subsequent dedicated inspection of suspicious spots on welds using the ultrasonic testing method phased array. This enables flaws to be clarified and the scope of repair to be defined.
Klaus Michael Fischer is innovation manager and technical director for fire and explosion prevention at TÜV SÜD Chemie Service GmbH