Why process safety and preventative maintenance go hand in hand
21 Mar 2022
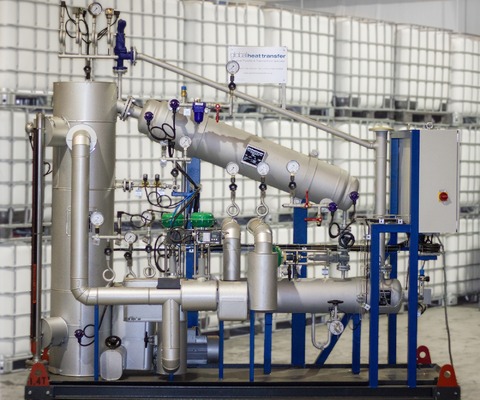
When operating a heat transfer system, the key to maintenance is dealing with the problem, not the symptoms, advises Clive Jones of Global Heat Transfer. Effective flash point management provides a good start...
When an issue arises in a heat transfer system, it should be solved as quickly as possible so that it does not negatively impact safety or production or result in unnecessary costs.
Take this example: during fluid sample analysis, engineers identify an increase in light ends in the fluid. Light ends boil and ignite at low temperatures, reducing the ignition point (flash point) of the thermal fluid. This increases the risk of fire, putting the workforce and facility at risk. Engineers can remove these light ends from the system, but if they do not deal with the cause of the problem, light ends will continue to be generated.
Heat transfer fluids operate at very high temperatures for extended periods of time, so if it is not monitored and managed properly, the fluid will begin to degrade and impact production.
When operated at these high temperatures, fluids begin to degrade as a result of oxidation — chemical reactions in the presence of oxygen. Oxidation produces sticky carbon deposits of sludge, which may be corrosive to a heat transfer system.
Fluid also degrades by thermal cracking. During cracking, the bonds between hydrocarbon chains break, producing shorter chained light ends that lower the flash point of the fluid. The higher the operating temperature, the more light ends are generated.
The rate at which the light ends are produced is also dependent on the oil type and the operating temperature. Hydrocarbon chains can also recombine to form heavy ends that usually cause fouling of the heat transfer system.
Engineers have a duty to manage light ends to reduce the risk of fire in line with legislation such as the Dangerous Substance and Explosive Atmospheres Regulations (DSEAR) and Explosive Atmospheres Directive (ATEX 137).
Engineers can temporarily install a light ends removal kit (LERK) to remove volatile light ends (see photo). Hot thermal fluid flows through the distillation vessel and the gaseous light ends are collected in the liquid phase of the condenser. The light ends are either drained automatically or manually from the system. The system is not open to atmosphere as a hot expansion tank would be. This protects the oil against oxidation ageing.
While removing the light ends will improve safety and productivity, if engineers do not deal with the cause of the formation of these light ends, the problem will reoccur.
Ongoing management
Implementing a continuous preventative maintenance can help to slow degradation and improve efficiency. Regular fluid sampling and analysis enables engineers to get an accurate representation of the condition of the fluid in the system and anticipate what could happen in the near future. Engineers can then intervene and carry out maintenance tasks before thermal fluid degradation impacts production, reducing the risk of downtime while also maintaining safe operations.
Permanently installing a LERK also enables engineers to manage light ends on a continuous basis; both passive LERKs that use gravity to return the oil to the circuit and a new range of active, floor mounted, LERKs that employ a frequency-controlled pump.
Clive Jones is managing director of Global Heat Transfer