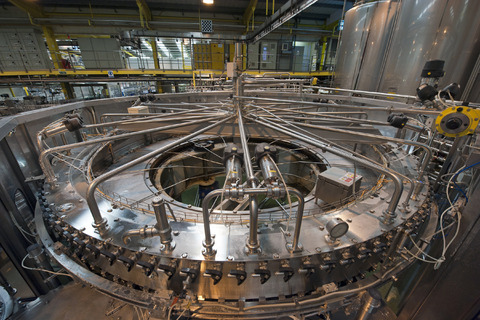
Nelson, UK – Cott Beverages has completed a project to resolve a level-sensing problem on a bottle-filling line at its plant in Nelson, Lancashire.
To meet high demand, Cott, which claims to be the world’s largest retailer-brand beverage company, operates its main processing stages, such as bottling lines on a virtually continuous basis.
Nearly 300 are employed at the Nelson site, which the company acquired when it bought out Macaw soft drinks in 2005. Since then the company has developed replacement strategies to deal with the challenges of maintaining legacy plant and overcoming parts obsolescence.
“We have a programme of replacing machinery and equipment over time, as the capital budget allows. We also need to get the best reliability and availability from existing plant, so good spares back-up is essential,” explains Ian Whitehead, plant electrical engineer:
“It’s critical to have suppliers who understand our processes in detail, so that technical information and support can help to keep the whole operation running smoothly,” he said.
Ensuring maximum up-time is a key priority on each of the five lines for still and carbonated drinks on the main Nelson facility, as well as two aseptic bottling lines housed in a separate plant on a neighbouring site.
On a typical multi-bottle filler, one litre and 500ml carbonated soft drinks like colas are bottled at around 19,000 units per hour, which allows a 40ms fill-time per unit. The syrup is mixed with water, carbonated, and then fed under pressure to the filling bowl, a ring-shaped header tank above the filling nozzles.
From here, actuated valves dispense the beverage into the bottle under gravity, and it is then capped, labelled and sent to packing.
The plant’s operations work to demanding targets, so maximum availability for every machine is essential. That means knowing where potential failures may happen and ensuring changeover and commissioning of parts does not impact on the operation during production runs.
One project involved the installation of new LFP Inox fluid level probes from Sick UK. It has demonstrated how a more strategic approach to replacement has delivered a solution with major potential benefits for the whole plant.
“Controlling the level of liquid in the filling bowl is critical to the process as it determines the accuracy of fill,” explains Ian. “Margins can be squeezed by a run of poor fill. The level-sensing equipment was around ten years old and faults were becoming more frequent.”
Three level sensors positioned around the ring bowl delivered analogue 4-20mA output signals which were averaged out by the PLC unit. The level was fed to the actuator which controls the fill of soft drink pumped to the filling bowl.
Risk of Failure
However if one sensor became faulty, or ceased to work, there was no indication of a problem. A false level reading could affect the whole of a production run, and the only indication of a possible fault came with a higher proportion of unacceptable fills.
In addition, identifying which sensor was faulty, replacing it, testing, calibrating and cleaning took around four hours of downtime, equating to the filling of about 80,000 bottles.
As each of the filling machines had different models and manufacturers of sensor, significant stock had to be kept, and suppliers were constantly being chased for spares, creating more delays. With the age of the sensing equipment, spares were becoming harder to source, leading to increased risk of downtime.
“We had reached the point where not only was the maintenance and replacement budget becoming too high, it was affecting operating margins for the whole plant,” said Ian.
“We decided that we should look for level sensing equipment which did a better job altogether, in terms of fault indication and the ability to compensate for faulty sensors should a problem occur.
“We identified that the newly-introduced Sick LFP Inox hygienic level sensors with IO link offered the improvements in performance and data output required. Our technical team then worked with Ian to determine the correct specification,” he said.
“The Sick support team is in regular contact with Ian and makes regular visits to site,” explains Wayne Morrison, the engineer responsible for Cott Nelson within Sick UK’s commercial goods team. “We identified that the newly-introduced Sick LFP Inox hygienic level sensors with IO link offered the improvements in performance and data output required. Our technical team then worked with Ian to determine the correct specification.”
“Connection to the three sensors is made via IO link. A single gateway enables connection of all three sensors to our Profibus network. This provides digital access to diagnostic data in each sensor allowing us to monitor whether an individual sensor is deteriorating, and an alarm can be triggered before any failure,” Whitehead explains.
“In the event of a fault developing with one of the sensors, the alarm and operator instructions on the filler’s HMI control panel facilitate the switching out of the faulty device.
“An average level of the two remaining sensors is maintained until an assessment can be made during routine maintenance downtime. The SICK LFP microwave sensors also have their own LED and digital readout, so we can pick up faults either on the HMI or on the filler bowl itself.”
The project team has completed a two-month run with the sensors on one filling machine without any incidents. An accuracy level of +/-1mm also delivered other operational benefits, particularly in improving the efficiency of the PID control of filling line pressure.
Based on the success of the trial, Cott’s strategy is now to use the same sensors on other filling machines to minimise spares stocks. The LFP Inox is ideal, because it has a stainless steel probe with a measuring length of between 300 - 2,000mm which can be cut to length on site to meet the required dimensions.
“We have a two-metre long probe which we can cut to fit each application,” Whitehead points out. “In addition, the LFP’s self-teach simplifies set up. This means we can fit the unit, press a button and it does the rest.
“Our trial runs showed we can complete a sensor replacement during the Clean In Place (CIP) phase between production runs.”
A one-hour CIP procedure is completed after every production run. Cleaning solution is fed automatically through the lines and filling plant at 65°C, and all equipment, such as seals and sensors, has to be able to withstand the detergents and the temperatures over many cycles.