Case study: steam distribution network reboot aids chemical firm
22 Nov 2016
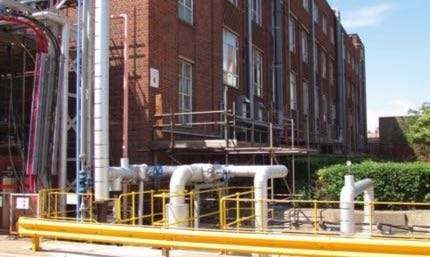
Chemical company reaps the cost and maintenance benefits of an upgraded steam distribution network at its plant in Middlesbrough.
Johnson Matthey is a speciality chemicals company that manufactures a wide range of products including emission control catalysts and active pharmaceutical ingredients (APIs).
Its technologies are designed to improve air quality, conserve natural resources and improve quality of life.
Globally, Johnson Matthey employs roughly 13,000 people and operates in more than 30 countries.
Recently it called on the services of Spirax Sarco, which specialises in steam system engineering, to overhaul the steam distribution network at its site in Billingham, near Middlesbrough.
Spirax Sarco worked alongside Johnson Matthey’s on-site operations and maintenance teams to reduce the length of steam line to approximately 25% of its original length
The work was undertaken during the summer shutdown period. Prior to the fix, the site’s processes and office heating was supplied by a neighbouring facility via an oversized steam line – 36 inches in diameter and more than one kilometre in length – which also lacked adequate steam traps, Johnson Matthey explains.
Crucially, the original system was not equipped with isolation valves either which meant Johnson Matthey’s maintenance teams were unable to shut down or isolate the flow of steam, the company adds.
Meanwhile, regular flange leaks were also leading to expensive maintenance bills and overall, the plant was suffering from heat losses that amounted to more than £130,000 per year.
Initially a pilot scheme was implemented to explore the potential value of proactive steam system maintenance.
Spirax Sarco worked alongside Johnson Matthey’s on-site operations and maintenance teams to reduce the length of steam line to approximately 25% of its original length before replacing the old 36-inch steam pipe with a new pipe made up of 8-inch and 4-inch sections.
The lesson we’ve taken from this project is that there are huge rewards to be had by challenging the way things have always been done
Chris McHale, gas services and operations team leader at Johnson Matthey
The pilot scheme was followed by the introduction of new control and automation devices including steam traps, dirt pockets and pressure indicators to improve the flexibility of use, and isolation valves offering much greater control of the steam supply itself.
Because of the overhaul, Johnson Matthey has made savings of approximately £60,000 per year on heat losses as well as reducing maintenance costs.
Commenting on the upgrade, Chris McHale, gas services and operations team leader at Johnson Matthey, says: “The lesson we’ve taken from this project is that there are huge rewards to be had by challenging the way things have always been done.
“Replacing a dated and problematic steam line with one much better suited to our current application may sound basic. But the cost, usability and safety benefits have proved second to none.”
Related Articles

Vetter expands storage for temperature-sensitive meds demand
Added: 12 Mar 2025
Manufacturer Vetter is on course to expand storage plant capacity at its Ravensburg facility in Ger…

Integrating legacy data in the pharmaceutical sector
Added: 12 Mar 2025
Pharmaceutical companies transitioning to electronic records need to be mindful that, convenient or…

Atlas Copco publishes new ebook guide to cooling systems
Added: 11 Mar 2025
Atlas Copco has launched a new downloadable guide for selecting the most appropriate cooling system…