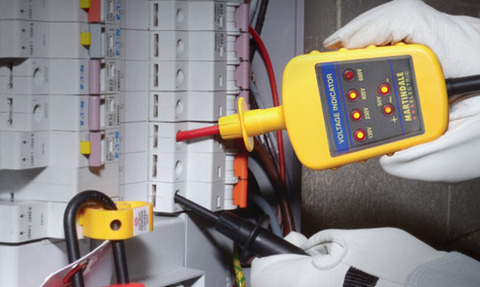
Electrical safety enforcement has got tougher. Avoiding injuries won’t suffice if you can’t prove compliance with the regulations, reports Brian Attwood.
A year ago last February, the UK Sentencing Council published its new guidelines on penalties for health and safety infringements.
Included were tougher recommended jail terms for serious offenders, with fines climbing steeply according to degree of culpability and turnover.
Electrical-related injuries and fatalities form a small but significant cohort of all cases where individuals are actually harmed; according to recent HSE stats, around 4% of fatalities and 1% of non-fatalities.
The consequence of the new guidelines is that the level of fines will be higher and custodial sentences more likely
Andrew Holland, director of marketing at Martindale Electric
However, warns Andrew Holland, director of marketing at Martindale Electric, the potential for companies to fall foul of the law is much greater than these figures suggest.
“New fines are structured not just to punish employers whose failure to comply results in serious injury, but also those whose lack of compliance put their employees at risk,” he says.
“The consequence of the new guidelines is that the level of fines will be higher and custodial sentences more likely. For the largest companies, who are judged to have a high level of culpability and the highest harm category, fines could be as high as £10 million.”
Planning ahead
Neil Dyson, business line manager – machinery at TUV-SUD Product Service [pictured below], has considerable experience of the issue, both in his present post and formerly as machinery safety consultant/ trainer for Pilz Automation Technology.
The good news, he says, is that the process industries are in a better state of preparation than most.
“What I do find is that the process industry tends to be better than industry per se, because they have a lot tighter grip on their controls – the lockout and tagout, for example.
“This is understandably so, as ‘industry’ equates to your standard factory, whereas process may involve petrochemicals but also healthcare, medical sites. But we still do find issues with these industries…”
On a regular basis and across sectors, says Dyson, his engineers visiting sites will pick up continuing issues with electrical safety – be it in a panel, PLC (programmable logic controller) or HMI (human-machine interface) systems.
Emergency checks and repairs may solve the immediate problem, agrees Dyson, yet can encourage a certain complacency “because people, once it’s fixed, tend to leave it alone unless something needs modifications”.
The challenge is to create a mindset that shifts reliance on emergency checks towards embedding workplace practices based on scheduled checks – in effect, opting for prevention rather than cure.
This of course requires a balanced approach to those key aspects including legislation, regulations, tools and training.
Getting it right does, says Dyson, come down to one thing primarily: PUWER, the Provision and Use of Work Equipment Regulations.
“For me the balance of factors to ensure safety [requires] they do PUWER because that covers all the aspects within training… and that’s a critical thing that I think a lot of people are overlooking.
“I go to sites and ask when is the last time they did PUWER and you know they’re not going to be able to answer because they’ve probably never done it.”
For me the balance of factors to ensure safety [requires] they do PUWER because that covers all the aspects within training… and that’s a critical thing that I think a lot of people are overlooking
Neil Dyson, business line manager – machinery at TUV-SUD Product Service
Whether the work being done is emergency or scheduled, if it requires the removal of standard guarding and the exposure of mechanical, electrical and other hazards, the isolation is always key, says the Health and Safety Executive (HSE).
Clarity should be provided with regards to the safety protocols and the circumstances in which these apply. The HSE cites the example of cleaning mixing machinery – while this is not a maintenance task, it may need to be completed under isolation.
Appropriate precautions
A formal permit to work must be issued, outlining the task to be completed and precautions that need to be in place. Issue, sign-off and check should be completed by an appropriate person who is not undertaking the task.
After that the rules require:
- Isolation from the power source
- The isolator should be locked in position
- Use of isolation devices must be designed specifically for the purpose
- Stored energy such as pneumatic power dissipated before work
- A sign displayed denoting isolation work in progress.
When it comes to the practicalities, Holland – who has two decades’ experience managing and developing test and instrumentation businesses – recommends careful attention to Electricity at Work Regulations HSG85.
These require maintenance of electrical plant and equipment to be carried out with circuits de-energised and locked off.
“Locking off the circuit which the equipment is connected to is just one part of the procedure. Before carrying out any work, you must verify that the circuit is dead.”
That is not always so clear-cut, warns Holland. In some instances where neutrals are ‘borrowed’ they can become live if an energised load on another circuit is connected to it.
“To prove dead, it’s essential to use a dedicated voltage indicator and a proving unit.”
How do people get themselves electrocuted? It’s usually when they are trying to do something right for the company, but unfortunately in the wrong way and perhaps not calling out an electrician
Neil Dyson, business line manager – machinery at TUV-SUD Product Service
These, together with locking off devices with unique keys and a clear method of labelling the hazard, form the essential test tools and equipment, explains Holland.
With a wide range of voltage detectors and indicators available, it’s important to understand that some equipment, such as multimeters, should not be used, he says.
Martindale’s own voltage indicators for safe isolation are fully compliant with the latest standards and are designed for safety, with no batteries or switches which could lead to false indication.
The latest VI-15000 voltage indicator has an over-voltage safety rating of 1,000V CAT IV, making it suitable for all installation categories and supply side applications, says Holland.
The advent of the high intensity LED has effected “probably the most significant development in test lamp design,” reckons Holland, and that has contributed in turn to improving electrical safety.
It has enabled the display of discrete voltages over a 360° viewing angle, even in bright sunlight.
“The visibility from all angles is unique when compared to conventional two-pole testers and makes for safer and easier voltage indication when carrying out safe isolation procedures,” explains Holland.
Detection devices
Test lamp are designed to be both lighter and tougher and often operate without batteries, ranges or switches, creating a simple way to prove dead before starting electrical maintenance.
Where technological advances are concerned, Dyson applauds the value of PLCs – “most of them are very good devices, they can be utilised to get fault detection immediately”. When it comes to specific equipment, mindful of his emphasis on preventing incidents rather than dealing with them retrospectively, Dyson is emphatic about the value of good protective devices.
“How do people get themselves electrocuted? It’s usually when they are trying to do something right for the company, but unfortunately in the wrong way and perhaps not calling out an electrician,” he says.
“Access to panels is probably one of the worse ones for me. That means these panels have got to be guarded and to be guarded they must be locked – and locked with a key that operators can’t get hold of.
“I’ll go to a panel and it’s already open and you’ve got a lot of current, probably at the bottom end coming in and do people understand it? I don’t think they do – it’s an invisible killer.”