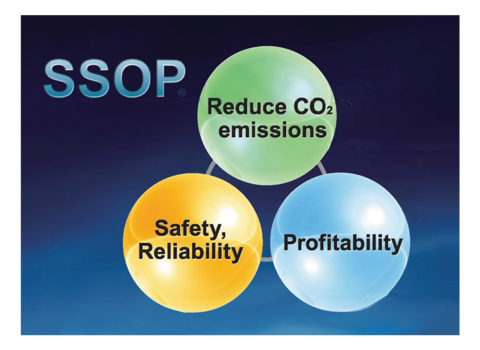
Originally intended for petrochemical plants and oil refineries, TLV’s Steam System Optimisation program (SSOP) has now been developed for other industries that have unique steam equipment and steam production equipment as an integral part of a process plant.
The production process, its feed and product streams are the lifeline of the plant and the steam system is intrinsic to the safe, reliable and profitable operation of a process plant. However, when it comes to the steam system a reactive strategy is generally adopted for maintenance and optimisation of the steam system, and, as a result, action is taken only after a problem becomes too severe to ignore.
However, there can be great rewards in proactively optimising the steam system. The SSOP is designed to optimise an entire steam system through visualisation. The aim is also to contribute to building a low-carbon society by minimising condensate problems, reducing steam losses and thereby reducing CO² emissions.
SSOP works in Three Phases:
- Phase 1 involves ‘best practice’ of steam trap management and the optimisation of all condensate discharge locations. This features the application of the BPSTM condensate discharge location management program to achieve and maintain the lowest possible failure rate in traps, valves and piping.
- Phase 2 involves ‘best practice’ of steam system management to optimise all steam applications, such as steam-using equipment and tracing. On site surveys can be performed to identify any gap between theoretical expectations of steam utilisation and actual plant operation.
- Phase 3 is the important balancing and optimisation of the entire steam system. This considers all interconnected parts of the total system as an individual asset and allows the visualisation of the whole to identify the most effective combination of improvement opportunities.
Increased reliability and productivity is then achieved for the client through important practical improvements such as the prevention of production bottlenecks, unexpected equipment failures and the elimination of water hammering, says the company.
Initial SSOP assessment can estimate benefits for an entire plant based on quantified benefits in assessed areas – leading to the development of a road map to the optimisation of the plant.
SSOP can help your plant…
Reduce CO2 Emissions by…
- Stopping steam loss
- Improving energy efficiency
Improve the safety and reliability of your plant by…
- Eliminating problems caused by condensate
- Eliminating water hammer
- Preventing unexpected equipment failures
- Improving equipment longevity
Increase the profitability of your plant by…
- Increasing production efficiency
- Reducing operating expenditure
- Mitigating production bottlenecks
For more information, click here.