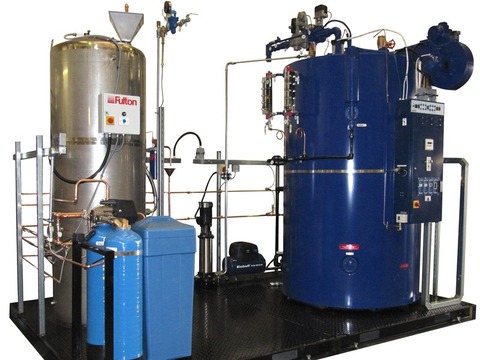
Fulton Limited, a British manufacturer of steam, hot water and thermal fluid solutions, has supplied three dual-fuel-fired, skid-mounted boiler systems – a 30J and two 40J – to cavity wall insulation specialist Domestic & General Insulation (DGI) and its wholly-owned processing subsidiary Thermabead.
Fulton Limited, a British manufacturer of steam, hot water and thermal fluid solutions, has supplied three dual-fuel-fired, skid-mounted boiler systems – a 30J and two 40J – to cavity wall insulation specialist Domestic & General Insulation (DGI) and its wholly-owned processing subsidiary Thermabead.
Formed in 1986, DGI is one of the largest insulation specialists in the UK and has, since 2005, been manufacturing its own cavity wall bead at its Worcester-based Thermabead facility, where the first Fulton skid-mounted steam boiler system – the 30J model - was installed.
With business growing rapidly thanks to government improvement grants for energy-saving home insulation and DGI winning support to promote the only programme able to offer a 20% more efficient carbon-saver bead, the company quickly expanded its installer and processing divisions and now has a manufacturing plant in Manchester (using the first of the 40J-based boiler systems), with a third facility – known as ‘Project X’ – currently in the planning stages.
Steam from the Fulton boilers is at the heart of the operation, playing a critical role in the Thermabead production process which, without it, would simply stop.
DGI is in the process of establishing a third production facility, which will feature the second 40J skid-mounted boiler system and, as well as a service contract plans to take advantage of Fulton’s recently introduced City & Guilds certified Operator Routines & Maintenance course, which will train its engineers on the boilers they will be operating on a day-to-day basis.
“Fulton has always reacted positively to any issues, even attending call-outs at weekends. The boiler systems are tremendously reliable, simple in operation and easy to understand. Fulton even offers our engineers training at the point of installation.” says Mark.
Much of DGI’s growth, and its success, has been attributed to the effectiveness of its surveying and the quality of the cavity wall product, which is unique and has been developed through a partnership between its processing subsidiary Thermabead, and BASF.
Mark Aston says the result – the ‘Diamondbead’ polymeric insulation product – is the most advanced and efficient bead available and is acknowledged by many in the industry as the best. He claims traditional polystyrene-based cavity wall products use round ‘tumble’ beads of different sizes that don’t properly interlock or provide enough air space, which is vital for insulation performance. Diamondbead is more uniform in its shape, which means it locks together to provide a better insulation value inside the cavity.
In its raw state, ‘Diamondbead’ looks like a grain of salt, so indirect steam from Fulton boilers is used to heat the polymeric bead to make it more malleable. Heat is also used to raise the temperature of the blowing agent (pentane gas), which forms polymer chains within the bead to make it ‘puff up’ (expand?) to the required densities.
In a typical week, 110 tonnes of the base polymeric beads are processed to produce approximately 103 tonnes of Diamondbead, the difference in weight being attributed to the loss of the pentane blowing agent. This volume is enough to insulate the cavity walls of up to 7,000 properties per week (a mix of housing association, local authority housing stock and private housing). Sixty percent of installations are carried out by DGI’s own installer network, with the additional 40% by the company’s customers.
The decision to specify skid-mounted systems for the Thermabead facilities was based on Fulton’s ability to respond to DGI extremely short lead-times and the need to move into each facility within a week! For this reason, Fulton’s specification and design also included flanged connections for the pipe work to enable the systems to be easily installed. In addition, the Series J boilers, which deliver proven reliability and performance, are built in Britain to BS2790 1992 Class 1 and are covered by a five-year warranty on the pressure vessel.
Dual-fuel boilers were specified initially as the gas supply at both Worcester and Manchester sites was insufficient. The problem is being addressed and Fulton is currently working to prepare the necessary pipe work. When the required gas supply is available, modulating burners will be retro-fitted to help reduce energy costs. However, even without modulating burners Fulton’s boilers are proving easy to control and linear in their steam output.
Fulton’s modulating burners feature a linkageless burner management system to operate two modulating actuators, one of which regulates the flow of gas; the other adjusts air flow to ensure optimum combustion across the boiler’s full firing range. To optimise combustion and output, each valve can be adjusted by as little as 0.1º. Thanks to the modulation burners the boiler is also more efficient, as a more consistent steam pressure is maintained.
Summarising for DGI, Mark Aston says: “A great of technology has been built into our Manchester and Project X facilities, making them the most advanced of their kind. In a very competitive market, this level of investment and the installation of Fulton boiler technology make us more efficient and ensures that our Diamondbead insulation sets new standards in the industry.”